На главную
6. СТАЛИ И СПЛАВЫ С ОСОБЫМИ ФИЗИЧЕСКИМИ СВОЙСТВАМИ
Жароупорные и жаростойкие стали. Во многих отраслях производства применяются стали, обладающие особыми, специальными, свойствами. В области теплотехники требуется сталь, обладающая достаточной прочностью и стойкостью при высокой температуре, например: подина электронагревательных печей, отдельные части топок, водонагревательные трубы паровых котлов высокого давления, лопатки паровых турбин, нагревательные элементы электропечей и т. д. Для этих целей применяют стали, обладающие жаростойкостью (окалиностойкостью) и жаропрочностью (высоким сопротивлением механическим нагрузкам при высоких температурах), в особенности при температуре свыше 580 — 600°С.
Жаростойкая сталь должна обладать такими свойствами, которые препятствовали бы образованию окисла. Хром, алюминий и кремний имеют большее сродство с кислородом, чем железо, поэтому прибавка этих элементов в сталь препятствует соединению железа с кислородом. Чем выше рабочая температура детали, тем больше указанных элементов должна содержать сталь.
Так, например, при 5% хрома сталь жаростойкая до температуры 700°С, при 7 — 8% хрома сталь жаростойкая при 800°С, при 15% хрома сталь жаростойкая при 900°С, а при 18 — 20% хрома сталь жаростойкая при 1000°С.
Во многих случаях требуется, чтобы сталь не только хорошо сопротивлялась окислению при высокой температуре, но и выдерживала механическую нагрузку (водонагревательные трубки паровых котлов, лопатки паровых турбин и турбокомпрессоров и т. д.). В обычной же стали при температуре свыше 250° прочность быстро падает.
Нержавеющие стали. Чистая углеродистая и низколегированная стали не устойчивы против коррозии (ржавления) как в атмосфере, так и в жидких средах ввиду того, что образующаяся пленка окиси недостаточно плотна и не изолирует металла от химического воздействия среды. Однако прибавкой в сталь специальных элементов в определенной пропорции можно создать сплав, практически не окисляющийся почти в любой среде (за исключением некоторых кислот).
Так, например, сталь, содержащая 12% хрома, практически не ржавеет в атмосфере и во многих других средах; сталь, содержащая хрома 14% и больше, практически ведет себя, как благородный металл, и не ржавеет во многих кислотах, солях и щелочах; сталь, содержащая хрома меньше 12%, подвергается коррозии почти также, как обычная углеродистая сталь.
Хромистые нержавеющие стали подвергаются коррозии только в соляной и серной кислотах. Хромоникелевые нержавеющие стали подвергаются коррозии в соляной кислоте, но устойчивы в серной кислоте.
Более высокими свойствами по коррозионной стойкости и жароупорности обладает сталь с содержанием хрома 18% и никеля 8%, так как эта сталь при всех температурах сохраняет аустенитную структуру, что обеспечивает хорошую ее обрабатываемость и малый рост зерна при нагреве.
В, тех случаях, когда деталь должна работать длительное время при температуре выше 650°С и в разъедающей среде, применяется хромоникелевая сталь указанного выше состава с прибавкой титана до 0,4 — 0,8%.
В табл. 37 приведен химический состав нержавеющих и жаростойких сталей.
Таблица 37
Химический состав нержавеющих и жаростойких сталей
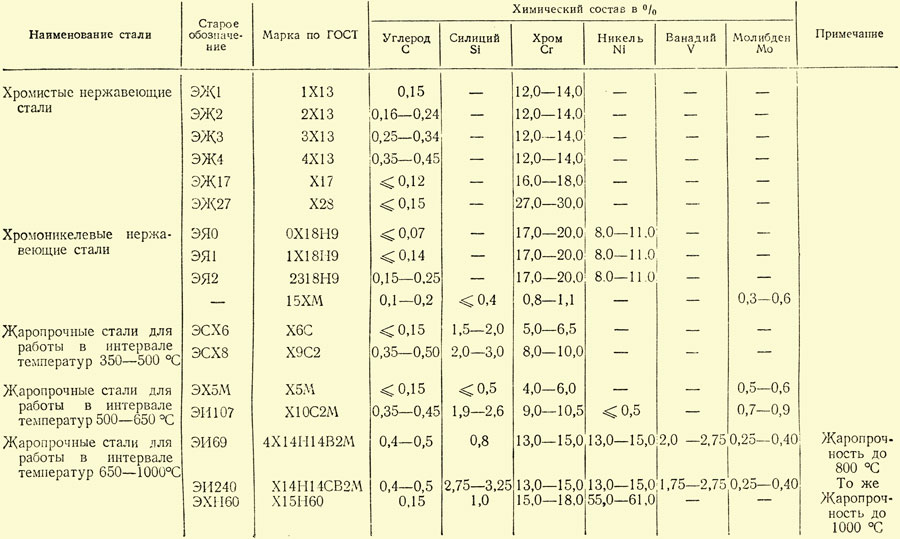
Износоустойчивые стали. Обычно принято считать, что износоустойчивая сталь должна иметь высокую поверхностную твердость, которая достигается специальной термообработкой (цементация, закалка, азотирование). Однако имеется сталь с поверхностной твердостью Нб = 200 — 250, но обладающая высоким сопротивлением истиранию. Этим свойством обладает высокомарганцовистая сталь (сталь Гадфильда) марки Г13, содержащая 1 — 1,3% С и 10 — 15% Мn. Эта сталь после закалки при температуре 1100°С в воде получает аустенитную структуру и имеет большую способность к наклепу. В процессе работы рабочая поверхность детали, подвергаясь ударам или давлению, наклепывается и тем самым увеличивает свое сопротивление истиранию. Этим также объясняется и то, что эта сталь весьма трудно обрабатывается резанием (резцом, зубилом) несмотря на незначительную твердость, так как при давлении резца или зубила поверхность стали получает высокий наклеп. Обычно детали из этой стали отливаются и обрабатываются только шлифовкой. Применяется эта сталь для различных деталей камнедробилок, рабочих частей (зубья) ковшей землеройных машин и т. д.
Сплавы высокого электросопротивления. Для реостатов и нагревательных элементов различных электронагревательных приборов и печей требуется сплав, обладающий высоким электросопротивлением, минимальным температурным коэффициентом электросопротивления, а для нагревательных элементов сплав должен обладать еще и окалиностойкостыо.
Для нагревательных элементов применяют сплавы: на никелевой основе — нихромы, на железной основе — фехраль; хромаль, меганир и т. д., в зависимости от температурного режима работы нагревательного прибора.
Сплавы, содержащие невысокий процент хрома и алюминия и обладающие жаростойкостью до температуры 1100°С, изготовляются в виде проволоки; сплавы с высоким содержанием хрома и алюминия с жаростойкостью до температуры 1250 — 1350°С не пластичны, из них изготовляются литые элементы сопротивления.
Химический состав сплавов приведен в табл. 38.
Таблица 38
Сплавы для нагревательных элементов
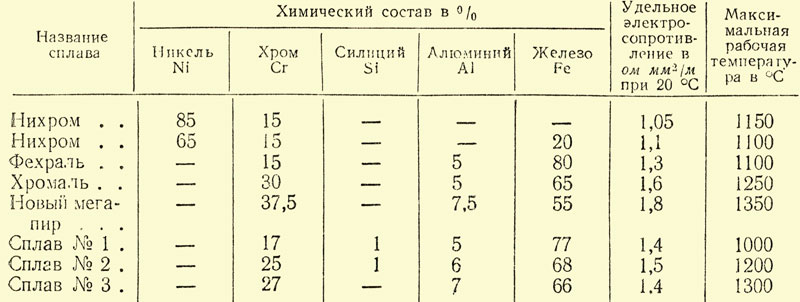
В приборостроении часто требуется, чтобы отдельные детали обладали определенным коэффициентом линейного расширения. В некоторых случаях требуется, чтобы коэффициент линейного расширения был минимальным (близким к нулю) или, наоборот, максимальным, имел определенное значение, или, наконец, этот коэффициент должен иметь определенное значение в заданном интервале температур. Для удовлетворения этих разнообразных требований, для каждого конкретного случая изготовляют сплавы строго определенного состава.
Обычно почти все металлы при нагреве расширяются по криволинейному закону, и с повышением температуры коэффициент линейного расширения (α) возрастает.
Этому же закону подчиняются и все сплавы металлов, за исключением сплавов Fe — Ni и Fe — Pt, в которых коэффициент линейного расширения не подчиняется общему правилу.
Так, сплав железа с 25% никеля имеет почти в два раза больший коэффициент линейного расширения, чем железо, а сплав железа с 36% никеля имеет в восемь раз меньший коэффициент линейного расширения, чем железо. Этот сплав имеет состав: 35 — 37% никеля, до 0,25% углерода и остальное железо и называется «инвар» (неизменный), практически не расширяющийся при нагреве до температуры 100°С.
Применяется он во многих приборах для деталей, которые не должны менять своих размеров с изменением температуры.
Сплав железа с 42% никеля имеет постоянное значение коэффициента а в интервале от 0 до 300°С, а сплав железа с 50% никеля — от 0 до 450°С.
В тех случаях, когда требуется, чтобы коэффициент линейного расширения сплава равнялся коэффициенту линейного расширения стекла (цоколь электрической лампочки и т. д.), применяют сплав, содержащий 48% никеля, названный «платинитом».
Детали, в которых требуется максимальный коэффициент линейного расширения изготовляют из сплава с 25% никеля, а детали приборов, у которых необходимо иметь максимальную деформацию при нагреве, делают из термобиметалла, представляющего собой две сваренные пластинки из сплавов Н25 и Н36 (содержащих 25% и 36% никеля). При нагреве пластинка коробится, потому что половина ее, изготовленная из сплава Н36, почти не расширяется, а другая половина, изготовленная из сплава Н25, расширяется очень интенсивно.
Для деталей с неизменным модулем упругости при изменении температуры (пружины точных приборов) применяют сплав, носящий название эльинвар (постоянная упругость), содержащий 36% никеля и 12% хрома.
Магнитные сплавы делятся на две основные группы:
1. Углеродистую сталь марок У10 — У12, которая применяется для небольших по размеру (сечением 5 — 7 мм2) неответственных магнитов.
2. Для более крупных магнитов применяют хромистую сталь.
Весьма высокие магнитные свойства имеют железоникельалюминиевые сплавы с содержанием никеля от 15 до 30% и алюминия до 13%. Этот сплав применяется для сильных магнитов малых габаритов и веса.
Для магнитов с переменным намагничиванием (например, сердечники трансформаторов) применяют сплавы, обладающие малым значением коэрцитивной силы и высокой магнитной проницаемостью, а если сплав в процессе работы подвергается намагничиванию переменным током, то должны быть малые потери на гистерезис и на возникающие токи Фуко.
Железо армко обладает низкой коэрцитивной силой и высокой магнитной проницаемостью, но имеет большие потери на токи Фуко. Поэтому применять его для изделий, подвергающихся переменному намагничиванию, нерационально. При добавлении в железо кремния коэрцитивная сила магнита изменяется мало, а электросопротивление сильно возрастает и потери на токи Фуко уменьшаются. В связи с этим для сердечников трансформаторов, динамомашин и т. д. применяют безуглеродистые сплавы с кремнием.
Трансформаторная сталь содержит около 4% кремния и минимальное количество углерода.
Для получения наибольшей магнитной проницаемости эту сталь отжигают при температуре 1000° в атмосфере водорода для выгорания наличного в стали углерода. Трансформаторная сталь имеет крупнозернистое строение и малую вязкость.
Динамная сталь, содержащая 1% кремния, имеет лучшую пластичность, чем трансформаторная сталь, но уступает ей по магнитным свойствам.
Для производства приборов (радио, телефон, телеграф и т. д.) требуется сплав с весьма высокой магнитной проницаемостью. Для этих целей применяют сплав пермалой, содержащий никеля 78,5%. Этот сплав до применения предварительно подвергается сложной термической обработке (двукратный нагрев до температуры 600 и 1 200°С в атмосфере водорода и остывание со скоростью 20° в сек.), которая и обеспечивает высокую магнитную проницаемость этого сплава.
предыдущая страница | Содержание | следующая страница |