На главную
3. МЕХАНИЧЕСКИЕ ИСПЫТАНИЯ МЕТАЛЛОВ
Испытания на растяжение. При испытании на растяжение можно определить предел прочности металла или материала, относительное удлинение, относительное сужение, предел упругости, предел пропорциональности, предел текучести и модуль упругости.
Однако практически чаще всего ограничиваются определением основных величин: предела прочности при растяжении, относительного удлинения и относительного сужения.
Если обозначить действующую на образец силу (нагрузку) Р кг, а площадь сечения образца F мм2, то напряжение
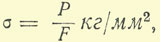
т. е. напряжение =
Напряжение, при котором материал при растяжении разрушается, называется пределом прочности при растяжении и обозначается σвр.
Если растягиваемый образец имел первоначальную площадь сечения F0 мм2 и разрывающую нагрузку Р кг, то предел прочности при растяжении
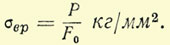
Относительное удлинение. При испытании на растяжение образец удлиняется пропорционально увеличению нагрузки. До определенной величины нагрузки это удлинение не является остаточным (фиг. 167), т. е. если снять в это время нагрузку, то образец примет первоначальное положение. При больших нагрузках (больше, чем в точке А) образец получает остаточное удлинение. Если сложить обе половинки образца после его разрушения, то общая длина образца l будет больше, чем исходная длина образца l0 до его испытания. Увеличение длины образца характеризует пластичность (тягучесть) металла.
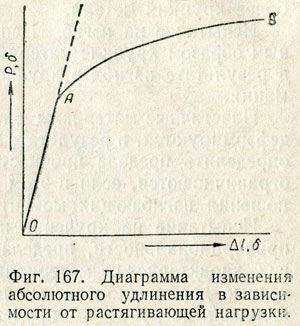
Обычно удлинение определяется в центральной части образца.
Относительное удлинение определяется отношением полученного при растяжении удлинения l — l0 к первоначальной длине образца l0 и выражается в процентах:
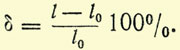
Относительное сужение — это отношение уменьшенной площади поперечного сечения образца после разрыва (F0 — F) к площади сечения образца до разрыва (F0)
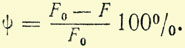
Испытание на удар. Для определения ударной вязкости материала (сопротивление его динамической — ударной нагрузке) применяют испытание образца материала на удар на специальной машине — маятниковом копре (фиг. 168). Для этого берут образец определенной формы и сечения с односторонней выточкой по середине, укладывают на опоры копра и ударом маятника с определенной высоты разрушают образец. По затраченной на разрушение образца работе определяют ударную вязкость материала. Чем меньше ударная вязкость, тем более хрупкий металл.
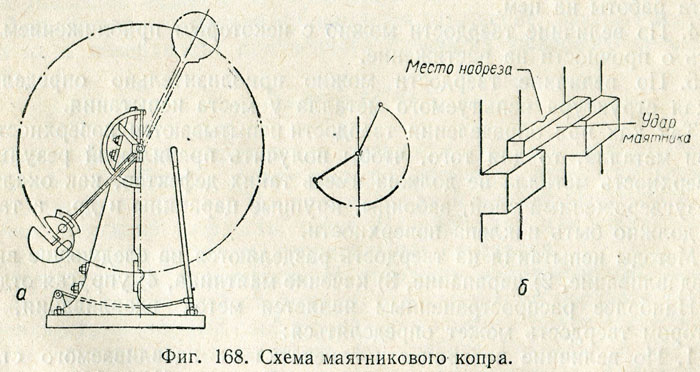
Испытание на изгиб. Испытанию на изгиб подвергаются главным образом хрупкие материалы (чугун, закаленная сталь), которые в результате изгиба разрушаются без заметной пластической деформации.
Пластичные материалы (малоуглеродистая сталь и др.) при изгибе деформируются, в результате изгиба не разрушаются и для них нельзя определить предела прочности при изгибе. Для таких материалов ограничиваются, если в этом есть необходимость, определением соотношения изгибающих моментов к соответствующим прогибам.
Испытание на кручение применяется для определения предела пропорциональности, предела упругости, предела текучести и других характеристик материала, из которого изготовляются ответственные детали (коленчатые валы, шатуны и др.), работающие при большой нагрузке на кручение.
Испытание на твердость. Из всех видов механических испытаний металлов испытание на твердость проводится чаще всего. Это объясняется тем, что испытание на твердость имеет ряд существенных преимуществ по сравнению с другими видами механических испытаний:
1. Изделие не разрушается и после испытания поступает в эксплуатацию.
2. Простота и быстрота испытания.
3. Портативность прибора для испытания на твердость и простота работы на нем.
4. По величине твердости можно с некоторым приближением судить о прочности на растяжение.
5. По величине твердости можно приблизительно определить, какая структура испытуемого металла у места испытания.
Так как при определении твердости испытываются поверхностные слои металла, то для того, чтобы получить правильный результат, поверхность металла не должна иметь таких дефектов, как окалина, обезуглероженный слой, забоины, крупные царапины и др., а также не должно быть наклепа поверхности.
Методы испытания на твердость разделяются на следующие виды: 1) вдавливание, 2) царапание, 3) качение маятника, 4) упругая отдача.
Наиболее распространенным является метод вдавливания, при котором твердость может определяться:
1. По величине поверхности отпечатка от вдавливаемого стального шарика при испытании на прессе Бринеля (фиг. 169).
2. По глубине отпечатка при вдавливании алмазного конуса или стального шарика при испытании на приборе Роквелла (фиг. 170).

3. По величине поверхности отпечатка от вдавливания алмазной пирамиды при испытании на приборе Виккерса.
При испытании твердости на прессе Бринеля в качестве твердого тела, вдавливаемого в испытуемый материал, применяется стальной закаленный шарик диаметром 10,5 или 2,5 мм. Детали толщиной более 6 мм испытываются шариком диаметром 10 мм при нагрузке 3000 или 1000 кг. Детали толщиной от 3 до 6 мм испытываются шариком диаметром 5 мм при нагрузке 750 и 250 кг. При испытании детали толщиной менее 3 мм применяют шарик 2,5 мм и нагрузку 187,5 кг. За меру твердости принимается отношение взятой нагрузки Р в кг к поверхности полученного отпечатка (шарового сегмента)
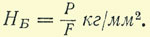
Для ускорения определения твердости по Бринелю имеются специальные таблицы, в которых по диаметру отпечатка (лунки) определяется твердость. На прессе Бринеля нельзя испытывать материал, имеющий твердость выше НБ = 450, так как шарик будет деформироваться и давать неправильные показания.
Нельзя также испытывать на твердость азотированный, цементованный и закаленный слой стали, так как шарик продавит тонкий поверхностный твердый слой и показания прибора будут искаженные.
При испытании на твердость на приборе Роквелла в качестве твердого тела, вдавливаемого в испытуемый материал, применяется алмазный конус с углом у вершины 120° или конус из твердого сплава или стальной закаленный шарик диаметром 1,59 мм (1/16").
Величина твердости представляет собой разность между глубиной впадин, получаемых на испытуемом предмете от вдавливания алмазного конуса под двумя нагрузками определенной величины: большей нагрузкой — основной и меньшей — предварительной. Предварительная нагрузка равняется 10 кг, а общая нагрузка, т. е. предварительная плюс основная, равняется при вдавливании стального шарика 100 кг (шкала В) и при вдавливании алмазного конуса — 150 кг (шкала С) или 60 кг (шкала А).
Измерение твердости шариком по шкале В применяется в том случае, когда твердость не велика (не закаленная или слабо закаленная сталь, бронза и т. д.). Алмазным конусом при нагрузке 60 кг по шкале А проверяют твердость цементованного и закаленного слоя (не глубокого), азотированного слоя, а также в тех случаях, когда нежелательно оставлять большого следа на изделии от наконечника, или, наконец, в тех случаях, когда измеряемая поверхность находится близко от рабочей кромки (режущие кромки развертки и т. д.).
Твердость на приборе Роквелла обозначается RB, Rc и Ra в зависимости от того, при какой нагрузке производится испытание, т. е. по какой шкале — В, С или А.
Показания твердости на приборе Роквелла являются условными, они не имеют той размерности, какую имеет прибор Бринеля.
Для перевода твердости по Роквеллу на твердость по Бринелю имеются переводные таблицы.
Во многих случаях необходимо определить твердость тонких предметов толщиной менее 0,3 мм, например, твердость тонкого азотированного слоя, твердость стержней малого сечения (спиральные сверла диаметром 1 мм и менее, режущие кромки разверток и т. п.). В таких случаях применяют прибор Виккерса. В этом приборе испытание ведут четырехгранной алмазной пирамидой с углом при вершине 136°. Нагрузка применяется в 5, 10, 20, 30, 50, 100 и 120 кг. .Малые нагрузки применяют для измерения твердости азотированного слоя тонких или мелких предметов. Во всех остальных случаях применяют повышенную нагрузку. Мерилом твердости на приборе Виккерса служит размер диагонали углубления пирамиды на испытуемом изделии. Размеры отпечатка пирамиды определяются при помощи специальной лупы с неподвижной и подвижной линейками. По размеру диагонали по специальной переводной таблице определяют твердость по Виккерсу. В обозначениях твердости по Виккерсу обязательно указывают, какая применялась нагрузка, например: HD5, HD30 и т. д. Числа твердости Но До 400 единиц совпадают с числом твердости НБ (при испытании на приборе типа Бринеля), а при твердости более 400 НD превышают числа НБ и тем больше, чем больше твердость.
Испытание на твердость динамическим вдавливанием шарика. Во многих случаях требуется определить хотя бы ориентировочно твердость металла крупных деталей, например, вала прокатного стана, шейки вала мощного двигателя, станины и других, которые не могут быть практически подведены под прибор Бринеля, Роквелла и Виккерса. В этом случае твердость определяют ориентировочно ручным прибором Польди (фиг. 171).
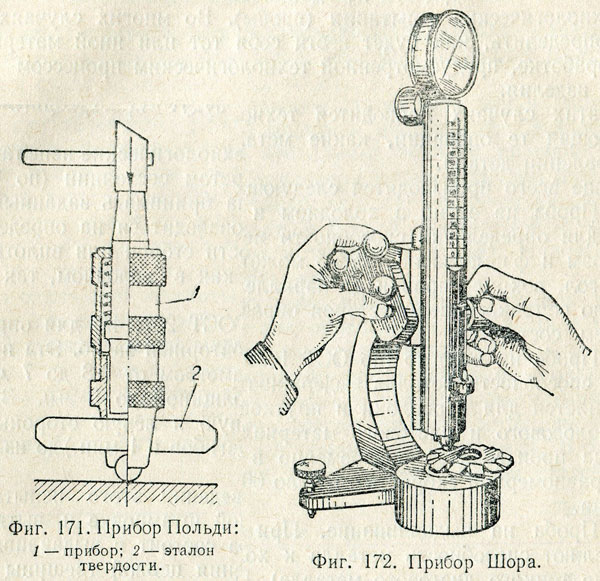
Устройство прибора Польди заключается в следующем: в специальной обойме находится шток (боек) с буртиком, в который упирается пружина, в нижней части штока имеется щель, в которую вставлен стальной шарик. В эту же щель вставляется эталон твердости — пластинка определенной твердости.
Такой переносный прибор устанавливают на деталь в том месте, где надо проверить твердость, и по верхней части бойка ударяют ручным молотком со средней силой один раз. После этого сравнивают размер лунки отпечатка на эталонном образце и на измеряемой детали, полученной одновременно от шарика при ударе в боек. Затем по специальной таблице определяют “число твердости детали.
В тех случаях, когда требуется определить твердость твердого закаленного металла без какого-либо следа от замера или определить твердость крупной закаленной детали, или, наконец, приближенную твердость закаленных шлифованных готовых деталей массового выпуска, применяют прибор Шора, основанный на принципе упругой отдачи (фиг. 172).
Принцип работы прибора Шора заключается в следующем: определенного веса боек с алмазным наконечником падает с высоты на измеряемую поверхность и благодаря упругости испытуемого металла отскакивает на определенную высоту, визуально фиксируемую на градуированной стеклянной трубке.
Точность показаний прибора Шора приближенная. Особенно неточно показывает прибор при испытании тонких пластинок или тонкостенных трубок, так как степень упругости тонкой пластинки или трубки и массивных деталей, имеющих большую толщину, при одной и той же твердости не одинакова.
Технологические испытания (пробы). Во многих случаях требуется определить, как будет вести себя тот или иной материал при его обработке, предусмотренной технологическим процессом изготовления изделия.
В этих случаях проводится технологическая проба, предусматривающая те операции, какие металлы будут претерпевать при изготовлении детали.
Чаще всего производятся следующие технологические испытания.
1. Проба на загиб в холодном и нагретом состоянии (по ОСТ 1683) для определения способности металла принимать заданный по размерам и форме загиб. Загиб может производиться на определенный угол, вокруг оправки до параллельности сторон или вплотную, т. е. до соприкосновения сторон образцов как в холодном, так и в горячем состоянии.
2. Проба на перегиб (по ОСТ 1688 и ГОСТ 2579-42) для определения способности металла выдерживать повторный загиб. Эта проба применяется для проволоки и прутков диаметром от 0,8 до 7 мм и для полосового и листового материала толщиной до 5 мм. Загиб образца производится попеременно в правую и левую стороны на 90° с равномерной скоростью (около 60 перегибов в 1 мин.) до излома образца.
3. Проба на выдавливание. При проведении этого испытания определяют способность металла к холодной штамповке и вытяжке (обычно тонкого листового металла). Проба состоит в выдавливании углубления в листовом металле до появления первой трещины под пуансоном, рабочий конец которого имеет полусферическую форму. Для проведения испытания применяют простые по конструкции ручные винтовые прессы.
Кроме указанных проб, материал может подвергаться и другим видам технологического испытания: расплющиванию, загибу сварных швов, загибу трубы и т. д. в зависимости от требований производства.
предыдущая страница | Содержание | следующая страница |