На главную
§ 40. КАЧЕСТВО ПОВЕРХНОСТИ
Общие понятия
На поверхности детали после фрезерования образуются неровности в виде чередующихся гребешков и впадин (шероховатость и волнистость), возникают остаточные напряжения в верхнем слое металла, меняется твердость на разной глубине от поверхности (упрочнение и наклеп) и происходят другие явления, влияющие на свойства поверхностного слоя деталей машин. Все перечисленные характеристики определяют качество поверхностного слоя или, сокращенно, качество поверхности деталей машин.
В технике принято качество обработанной поверхности рассматривать с физической и геометрической сторон.
Физическое качество поверхности
Качество обработанной поверхности определяют отклонениями физических и механических свойств верхнего слоя металла от свойств металла в сердцевине детали.
При резании поверхностный слой детали претерпевает пластические деформации, поэтому его свойства оказываются отличными от свойств исходного металла (заготовки). Металл в этом слое оказывается упрочненным, его твердость повышается, в нем возникают внутренние напряжения.
При чистовом фрезеровании толщина упрочненного слоя не превышает нескольких сотых миллиметра, при черновом фрезеровании цилиндрической фрезой достигает 0,12 мм (средние значения 0,04—0,08 мм) и при черновом фрезеровании торцовой фрезой 0,2 мм (средние значения 0,06—0,10 мм).
Упрочнения и внутренние напряжения в поверхностном слое понижают усталостную прочность детали и вызывают ускоренное разрушение ее в работе, т. е. приводят к необходимости ремонта.
Поэтому фрезеровщик должен стремиться при обработке не применять затупленного инструмента, уменьшать при помощи интенсивного охлаждения температуру в зоне резания, по возможности разделять съем припуска на черновой и чистовой переходы, не увеличивать без необходимости подачу на зуб фрезы.
Микрогеометрия поверхности
Неровности на поверхности детали, получающиеся после грубой обработки при больших подачах на зуб и глубине резания, видны и легко ощутимы пальцем. Неровности после получистовой и чистовой обработки при малой подаче на зуб и небольшой глубине резания незаметны для невооруженного глаза и почти не ощутимы пальцем.
Геометрическое качество поверхности в смысле наличия на ней гребешков, впадин, штрихов и других неровностей на ее малых участках называется микрогеометрией поверхности. На микрогеометрию поверхности при фрезеровании в основном влияют следующие факторы:
1) режим фрезерования (скорость резания, подача на зуб, глубина резания, род охлаждаемой жидкости);
2) вибрации вследствие недостаточной жесткости станка, приспособления, инструмента и детали;
3) геометрия, качество, состояние заточки и износ зуба фрезы (трение задней поверхности зуба об обработанную поверхность);
4) механические свойства обрабатываемого материала и материала инструмента.
Современное машиностроение с большими скоростями движущихся деталей машин предъявляет весьма высокие требования к чистоте поверхностей деталей машины.
Критерий оценки микрогеометрии поверхности
Для объективного суждения о степени шероховатости (микрогеометрии) поверхности после механической обработки деталей служит Государственный общесоюзный стандарт «Шероховатость поверхности» (ГОСТ 2789—59). В этом стандарте в отличие от ранее действовавшего ГОСТ 2789—51 для оценки шероховатости приняты три критерия:
среднее арифметическое отклонение профиля Rа, высота неровностей Rz и базовая длина l участка поверхности.
Подробнее о шероховатости поверхности излагается в курсе "Допуски и технические измерения".
Таблица 12
Классы чистоты поверхности
(по ГОСТ 2789 - 59)
Класс чистоты поверхности | Обозначение | Среднее ариф- метическое отклонение профиля Rа в мк | Высота неровностей Rz в мк | Базовая длина l в мм |
не более | ||||
1 2 3 | ![]() ![]() ![]() | 80 40 20 | 320 160 80 | 8 |
4 5 | ![]() ![]() | 10 5 | 40 20 | 2,5 |
6 7 8 | ![]() ![]() ![]() | 2,5 1,25 0,63 | 10 6,3 3,2 | 0,8 |
9 10 11 12 | ![]() ![]() ![]() ![]() | 0,32 0,16 0,08 0,04 | 1,6 0,8 0,4 0,2 | 0,25 |
13 14 | ![]() ![]() | 0,02 0,01 | 0,1 0,05 | 0,08 |
Примечание. Для классов чистоты 6 - 12 основной является шкала Ra, для классов 1 - 5, 13 и 14 - шкала Rz.
Подобно ранее действовавшему ГОСТ 2789—51 вновь введенный с 1 января 1962 г. ГОСТ 2789—59 предусматривает 14 классов чистоты поверхности, для которых максимальные числовые значения шероховатости Ra или Rz при базовых длинах l должны соответствовать указанным в табл. 12.
Обычно назначение чистоты поверхности при изготовлении деталей устанавливается по шкале классов чистоты.
Для обозначения всех классов чистоты устанавливается один знак — равносторонний треугольник . Рядом с треугольником указывается номер класса, например:
7,
8,
14.
Шероховатость поверхностей грубее 1-го класса обозначается знаком , над которым указывается высота неровностей в микронах, например
.
Обеспечение заданной чистоты поверхности и контроль
Чистота поверхности детали, необходимая для работы данного узла механизма или машины в целом, проставляется на чертеже в соответствии с правилами изготовления чертежей. Задача фрезеровщика — обеспечить требуемую чистоту в процессе обработки поверхности.
Фрезерование с заданной чистотой поверхности по 2 и 3-му классам ( 2,
3) не представляет затруднений и легко достигается при черновой обработке.
Чистоту поверхности по 4, 5 и 6-му классам ( 4,
5 и
6) сравнительно легко можно получить при цилиндрическом и торцовом фрезеровании при работе на исправном оборудовании, при жестком закреплении заготовок и незатупленной фрезе. Необходимая чистота поверхности достигается соответствующим уменьшением подачи либо увеличением скорости резания.
Для получения чистоты поверхности по 7 и 8-му классам ( 7 и
8) приходится выбирать геометрию фрезы, (число зубьев для цилиндрической фрезы, φ и φ1 для торцовой фрезы) и назначать соответствующие режимы фрезерования.
Контроль чистоты полученной поверхности обеспечивается непосредственным измерением микронеровностей или сравнением с образцами.
В цеховых условиях применяют эталоны, выпускаемые отечественньими заводами для 4, 5, 6 и 7-го классов чистоты (рис. 175), они дают возможность определить чистоту поверхности до 7-го класса в пределах ошибки на один класс.
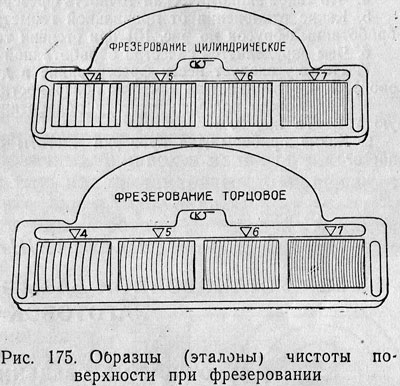
Применение лупы с 5—10-кратным увеличением дает возможность сравнения поверхностей примерно до 8—9-го класса чистоты с той же погрешностью в пределах одного класса. Полные наборы эталонов должны быть в центральной измерительной лаборатории завода, технологическом и конструкторском отделах завода. В бюро цехового контроля должны быть только эталоны, характерные для поверхностей деталей, изготовляемых в цехе. Такие эталоны необязательно хранить на рабочем месте. Рекомендуется при обработке партии заготовок с заданной чистотой поверхности изготовить первую пробную деталь по эталону с поверхностью заданного класса и затем изготовлять остальные детали по пробной детали, как образцу.
Образцовые детали целесообразно применять в случаях, когда проверяемые детали имеют сложную форму, которую трудно воспроизвести на эталонах (криволинейные очертания, переходные кривые) или когда цех (производственный участок) имеет узкую номенклатуру выпускаемых деталей ответственного назначения.
Для получения надежных данных при контроле методом сравнения с деталями-образцами необходимо по возможности выполнение следующих условий:
1) образцовая деталь должна быть изготовлена из того же материала, что и проверяемая деталь;
2) способы обработки поверхностей образца и детали должны быть одинаковыми, так как поверхности с одним и тем же классом чистоты, но полученные при различных видах обработки (фрезерование и строгание) имеют различные специфические штрихи неровностей.
Контроль методом сравнения с образцами — надежный производственный метод. Ошибки определения этим методом чистоты поверхности для 2—9-го классов не превышают половины допуска класса.
Для определения численной величины шероховатости поверхности существуют приборы, основанные на методе ощупывания проверяемой поверхности. В этих приборах применяется алмазная игла с очень малым радиусом закругления вершины, равным 2—3 мк. Игла с небольшим давлением перемещается по поверхности детали.
Приборы, показывающие непосредственно шероховатость поверхности, называют профилометрами. Приборы, записывающие шероховатость в виде увеличенного в пределах от 500 до 5000 раз профиля проверяемой поверхности (профилограммы), называют профилографами. Профилометры и профилографы применяют для лабораторного исследования чистоты обработанной поверхности.
1. Чем характеризуется точность обработанной детали?
2. Что влияет на неточность (погрешности) фрезерной обработки?
3. Как увеличить жесткость фрезерного станка, на котором вы работаете? Как увеличить жесткость оправки с надетой фрезой? Как увеличить жесткость заготовки, зажатой в тисках с большим вылетом?
4. Что такое экономическая точность фрезерной обработки?
5. Какие отклонения от правильной геометрической формы может иметь обработанный брусок по рис. 101 при степени точности 3 по табл. 9, 10 и 11?
6. Чем определяется качество обработанной поверхности?
7. Почему следует вести фрезерование в два перехода (черновой и чистовой)? Как это влияет на качество поверхности?
8. Как можно получить чистоту обработанной поверхности бруска, равную 6? То же,
8?
9. Какие приборы для проверки чистоты обработанной поверхности вы знаете?