На главную
§ 71. ПРОВЕРКА ТОЧНОСТИ ФРЕЗЕРНЫХ СТАНКОВ
Понятие о нормах точности
Детали каждого станка при механической обработке изготовляют с неизбежными отклонениями, вследствие чего абсолютная точность работы станка невозможна. Неточность фрезерного станка вызывает неточность обработки деталей, изготовляемых фрезерованием.
Для обеспечения предусмотренных системой допусков и посадок отклонений от заданных размеров допустимые неточности фрезерных станков регламентируются.
В настоящее время в СССР действуют нормы точности, установленные для новых консольно-фрезерных станков общего назначения (ГОСТ 13—54), которые обеспечивают точность обработки по 2-му классу и нормы точности для станков повышенной точности (ГОСТ 154—41 и 155—41).
По мере износа и истирания деталей станка в процессе работы точность его понижается. Точность станка восстанавливается при его ремонте, поэтому для консольно-фрезерных станков общего назначения, выходящих из ремонта, устанавливаются те же нормы точности, что и для новых станков.
Инструменты и приборы, применяемые для проверки точности станков
Для определения точности станков применяют следующий измерительный инструмент: проверочные линейки с широкой рабочей поверхностью и лекальные линейки, проверочные угольники, щупы, уровни, индикаторы и контрольные оправки.
Один конец контрольной оправки представляет собой конус, соответствующий конусу в гнезде шпинделя проверяемого станка, а другой конец сделан цилиндрическим. Контрольные оправки бывают диаметром 25, 40 и 60 мм при длине цилиндрической части соответственно 150, 300 и 500 мм.
Примеры проверки и нормы точности
Ниже дается несколько приемов проверки точности горизонтально- и вертикально-фрезерных станков, которые должен уметь выполнить каждый работающий на фрезерном станке, чтобы вовремя заметить неполадки станка, влияющие на качество и точность работы.
1. Проверка плоскостности рабочей поверхности стола. На рабочую поверхность стола по различным направлениям кладут линейку поверочной гранью на две калиброванные плитки равной высоты. Щупом и плоскими плитками (концевые меры длины) проверяется просвет между нижней гранью линейки и поверхностью стола. Допускаемое отклонение: 0,03 мм на длине 1000 мм в любых направлениях (допускается только вогнутость).
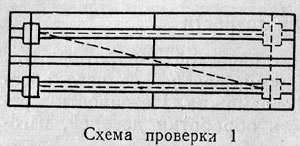
2. Проверка радиального биения оси конического отверстия шпинделя. Индикатор закрепляется на неподвижной части станка так, что его измерительный штифт касался цилиндрической поверхности концевой контрольной оправки, вставленной коническим хвостовиком в гнездо шпинделя. Шпиндель приводится во вращение. Измерение производится у торца шпинделя и на расстоянии L от торца шпинделя. Допускаемое отклонение: 0,010 мм у торца шпинделя; 0,020 мм на расстоянии L = 300 мм для станков первого, второго и третьего размеров.
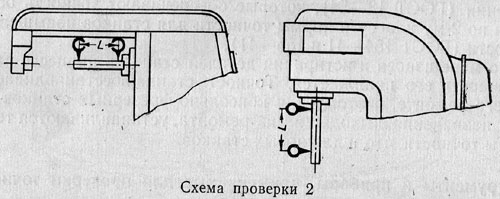
3. Проверка радиального биения наружной цилиндрической посадочной поверхности переднего конца шпинделя. Индикатор закрепляют на неподвижной части станка так, чтобы его измерительный штифт касался наружной поверхности переднего конца шпинделя, центрирующей насадные фрезы. Шпиндель приводится во вращение. Допускаемое отклонение: для станков первого, второго размеров и выше 0,015 мм.
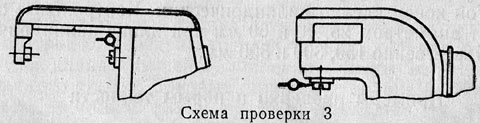
4. Проверка параллельности рабочей поверхности стола направлению его продольного перемещения. Индикатор закрепляется на неподвижной часта станка так, чтобы его измерительный штифт касался рабочей поверхности стола. Стол перемещают по продольным направляющим на всю длину хода. Консоль застопорена на станине;, а салазки — на консоли. Допускаемое отклонение на всей длине хода стола: до 300 мм — 0,015 мм, до 500 мм — 0,020 мм, до 1000 мм — 0,030 мм.

5. Проверка параллельности рабочей поверхности стола направлению его поперечного перемещения. Индикатор закрепляется на неподвижной части станка так, чтобы его измерительный штифт касался рабочей поверхности стола. Стол перемещают по поперечным направляющим на всю длину хода. Консоль застопорена на станине. Допускаемое отклонение на всей длине хода стола: до 300 мм — 0,020 мм, до 500 мм — 0,030 мм (стол может иметь отклонение только к станине).
6. Проверка параллельности оси вращения шпинделя рабочей поверхности стола. В коническое гнездо шпинделя вставляется консольная контрольная оправка. Измерение производится индикатором; основание стойки индикатора перемещается по рабочей поверхности стола, перпендикулярно оси оправки, таким образом, чтобы его измерительный штифт касался цилиндрической поверхности снизу или сверху оправки сначала у торца шпинделя, а потом на расстоянии L от него. Каждое измерение производится по двум диаметрально противоположным сторонам оправки в данном соединении ее со шпинделем, т. е. после первого измерения шпиндель вместе с оправкой поворачивают на 180°. Погрешность каждого измерения определяется средней арифметической результатов обоих замеров, по диаметрально противоположным сторонам оправки. Измерение производится в верхнем и нижнем положениях стола при застопоренных на станине консоли и салазках на консоли. Допускаемое отклонение: 0,03 мм на длине 300 мм для станков с шириной стола свыше 160 мм (свободный конец оправки может отклоняться только вниз).
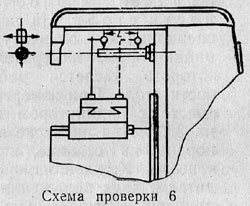
7. Проверка параллельности направляющих хобота оси вращения шпинделя в вертикальной и горизонтальной плоскостях. Индикатор закрепляют на специальной ползушке на хоботе так, чтобы его измерительный штифт касался цилиндрической части консольной контрольной оправки, вставленной в гнездо шпинделя. Ползушку с индикатором передвигают по направляющим хобота. Измерение производится в вертикальной И горизонтальной ПЛОСКостях. В каждой из плоскостей измерение производится по двум диаметрально противоположным сторонам оправки, для чего после первого измерения шпиндель поворачивают на 180°. Погрешность определяется средней арифметической результатов обоих измерений. Допускаемое отклонение: 0,025 мм на длине 300 мм для станков с шириной стола свыше 160 мм как в вертикальной, так и в горизонтальной плоскостях.
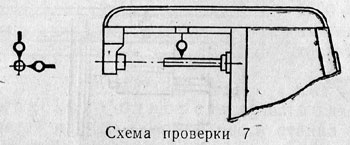
8. Проверка перпендикулярности оси вращения шпинделя к рабочей поверхности стола. На шпинделе крепят специальную коленчатую оправку с индикатором, измерительный штифт которого касается рабочей поверхности стола. При измерении шпиндель вместе с индикатором поворачивают на 360°. При проверке консоль застопорена на станине, а салазки — на консоли. Каждое измерение производится в двух положениях индикатора, смещенных относительно шпинделя на 180° в продольной и поперечной плоскостях. Погрешность каждого измерения определяется средней арифметической результатов обоих замеров, т. е. замеров при диаметрально противоположных положениях индикатора относительно шпинделя. Измерение производится в верхнем и нижнем положениях как стола, так и шпинделя (у станков с вертикальным перемещением шпиндельной бабки). У станков с поворотной шпиндельной бабкой она устанавливается в нулевое положение. Допускаемое отклонение: для станков с шириной стола свыше 160 мм на диаметре 300 мм — 0,020 мм в продольной плоскости и 0,030 мм в поперечной (в поперечной плоскости допускается наклон только в сторону станины).
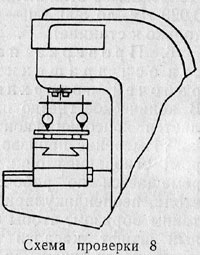
9. Проверка перпендикулярности рабочей поверхности стола к направлению вертикального перемещения консоли в продольной и поперечной плоскостях. Индикатор закрепляют на неподвижной части станка так, чтобы его измерительный штифт касался вертикальной рабочей грани угольника, установленного вдоль стола и поперек стола. Консоль перемещают по направляющим станины. Допускаемое отклонение: для станков с шириной стола свыше 160 мм на длине 300 мм — 0,020 мм вдоль продольной оси стола и 0,030 мм вдоль поперечной оси стола (в продольной плоскости отклонения могут быть в обе стороны, а в поперечной плоскости верхний конец угольника может отклоняться только в сторону станины).
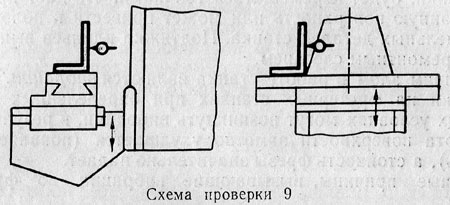