На главную
8. МЕХАНИЗАЦИЯ СБОРОЧНЫХ РАБОТ
В сборочные работы входит много простых, но трудоемких ручных операций, которые можно механизировать. Одной из таких операций является завертывание гаек, болтов, винтов, шурупов и шпилек.
Для выполнения этих операций применяют электрические и пневматические гайковерты, которые имеют набор наконечников для навинчивания гаек, винтов, шурупов, болтов. Производительность их в 3 — 10 раз выше производительности ручной работы. Гайковерты имеют специальные регулируемые на определенное усилие предохранители от чрезмерно большого крутящего момента, при котором можно сорвать резьбу или свернуть головку винта, шурупа, болта.
Техническая характеристика гайковертов
Заводская марка |
ФД-123 |
ФД-113 |
Техническая характеристика гайковертов повышенной частоты
Заводская марка |
И-60 |
И-61 |
И-63 |
Кроме указанных электрических и пневматических гайковертов, для завинчивания болтов, шпилек и гаек применяются различной формы ключи специального назначения и универсальные ключи.
Специальные ключи применяются для навинчивания гаек и завинчивания шпилек в труднодоступных местах. Для этих целей наиболее часто применяются торцевые прямые и изогнутые ключи с воротком или с трещоткой, шарнирные ключи, ключи с передвижной рукояткой и многогранные ключи. Для завинчивания гаек применяются коло-воротные ключи со сменными наконечниками (головками), что резко увеличивает производительность труда.
Для завинчивания шурупов и винтов применяют механическую отвертку, показанную на фиг. 104.

Для завинчивания гаек с определенным усилием применяют предельные гаечные ключи, в корпусе которых имеется пружина, регулируемая и устанавливаемая на требуемое усилие.
При монтаже (посадке) шариковых и роликовых подшипников на шпиндели, валы и валики применяют различное оборудование и приспособления, в зависимости от характера производства и объема выпускаемой продукции.
На производстве, где удельный вес монтажа и демонтажа подшипников велик, пользуются ручным или механическим прессом, а также упрощенной оснасткой — оправками, упорными кольцами и т. п.
Обычно шариковые подшипники перед посадкой их на вал тщательно промывают в чистом керосине и насухо вытирают. До запрессовки подшипники укладывают в сетчатую корзинку и погружают в масляную ванну, подогретую до температуры 80 — 90° С. Подогрев подшипников намного облегчает его посадку на вал. Масляные ванны обогревают паром, пропускаемым через згтеевик, при помощи электричества или иным способом.
Запрессовка шарикоподшипника на вал производится под прессом при помощи специального стакана, который досылает подшипник на свое рабочее место.
При отсутствии пресса или невозможности его применения посадку подшипника производят при помощи того же стакана легким постукиванием по нему.
При посадке подшипника внутрь детали нагревают корпус детали в масляной ванне (если деталь не велика). В случае возникшей необходимости демонтажа подшипника применяют специальные съемники, а иногда и пресс.
Форма съемника зависит от места расположения подшипника и удобства захвата его съемником. Конструкция одного из съемников подшипников качения приведена на фиг. 105.
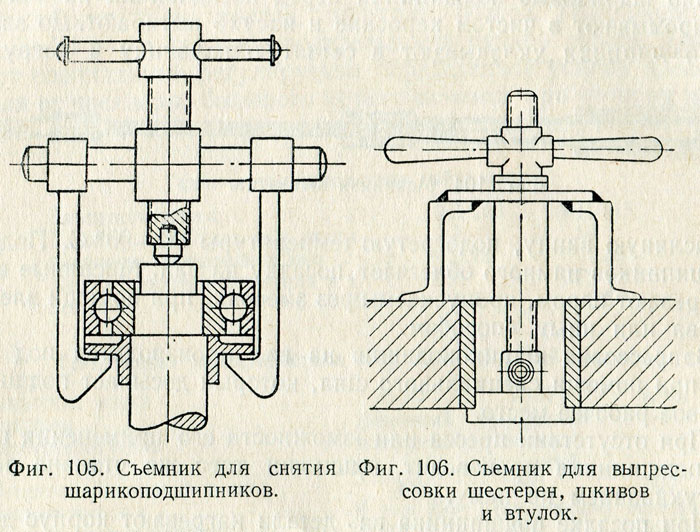
При запрессовке втулок, шестерен, звездочек и других аналогичных деталей пользуются различными способами. Основные из них следующие:
1) с помощью ручных прессов гидравлических и пневматических;
2) при помощи приспособлений (оправок, стаканов и т. п.) с применением молотка;
3) воздействием статической нагрузки (груза);
4) при помощи различных винтовых приспособлений;
5) путем нагрева детали (втулки), подлежащей запрессовке на вал;
6) путем охлаждения запрессовываемой детали;
7) при помощи нагрева одной детали (втулки) и охлаждения другой детали (валика).
Применение того или иного способа запрессовки зависит от условий и объема производства. При большом объеме производства нагрев деталей производят токами высокой частоты на специальной установке.
Если при запрессовке требуется охлаждение охватываемой детали, то это производится в жидком воздухе, жидком азоте или в твердой углекислоте (сухой лед). Температура охлаждения для жидкого воздуха и азота 190 — 196° С ниже нуля, а температура твердой углекислоты 75 — 80° С ниже нуля.
Способ запрессовки детали с предварительным охлаждением имеет следующие преимущества по сравнению с другими способами:
1 )высокая прочность соединения сопрягаемых деталей;
2) деформация запрессовываемых деталей меньшая, чем при других способах;
3) в процессе посадки на детали не образуются задиры;
4) структура металла улучшается;
5) время на посадку сокращается в 5 — 6 раз, по сравнению с другими способами.
Этот способ позволяет производить запрессовку длинных тонкостенных втулок (до 1500 мм) большого диаметра.
В случаях, когда посадка деталей производится с большим натягом, применяют комбинированный способ, т. е. подогревают охватывающую деталь и охлаждают охватываемую деталь.
Выпрессовка деталей (в случае необходимости) производится специальными приспособлениями, по конструкции аналогичными приспособлениям для выпрессовки подшипников.
На фиг. 106 показано приспособление для выпрессовки втулок.
Для механизации ручного труда слесаря-монтажника широко используются пневматические молотки (фиг. 107), которые применяются для пробивки сквозных отверстий, при клепке, чеканке, очистке литья и других работах.
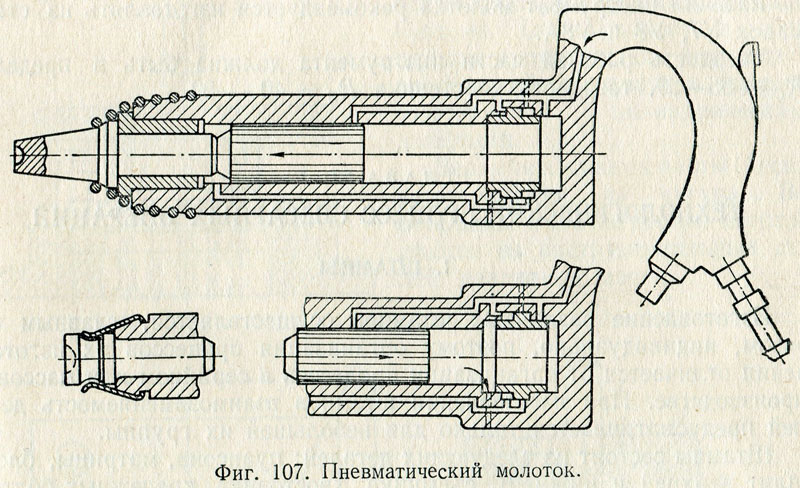
Простота конструкции, небольшой вес, большая энергия ударов (при значительной их частоте) обеспечивают преимущество пневматических молотков по сравнению с электрическими молотками.
Пневматические молотки изготовляются пяти размеров, отличающихся друг от друга по длине ударника и величине ствола.
Пневматический молоток представляет собой машину ударного действия.
Главными частями его являются: ствол с ударником, распределительный механизм с золотниковой коробкой и пусковым механизмом, рукоятка с шлангом для сжатого воздуха. В отверстие ствола вставляется рабочий инструмент (зубило, пуансон и др.), непосредственно производящий работу.
Внутри ствола и рукоятки имеются каналы для подвода и удаления сжатого воздуха.
Принцип работы пневматического молотка заключается в следующем. Когда нажимают на курок, вентиль открывает доступ сжатому воздуху из шланга в распределительный механизм молотка. В зависимости от положения ударника и золотника в момент пуска сжатый воздух проходит либо в камеру рабочего хода, либо в камеру обратного хода.
В том случае, когда золотник находится в крайнем положении, воздух поступает в камеру рабочего хода (слева от ударника) и движет ударник вправо до момента удара о хвостовик инструмента. В этот момент происходит рабочий ход ударника. В конце рабочего хода ударник открывает выхлопные каналы в стволе, давление в камере рабочего хода резко падает и вследствие этого золотник автоматически перебрасывается в крайнее левое положение. При этом открывается доступ сжатого воздуха в камеру обратного хода (справа от ударника) и происходит обратный ход ударника. В конце обратного хода ударник сжимает отработавший воздух в камере рабочего хода и уравновешивает золотник.
Когда в камере обратного хода произойдет выхлоп и резко упадет давление, золотник, теряя равновесие, перебрасывается обратно в крайнее правое положение, т. е. вновь начинается рабочий ход.
Рабочий инструмент молотка рекомендуется изготовлять из стали марок У7, У8 и У8А.
Твердость рабочей части инструмента должна быть в пределах Rc = 56 — 59, твердость хвостовика Rc = 40 — 50.
предыдущая страница | Содержание | следующая страница |