На главную
2. СВАРКА
Сварка применяется для соединения металлических деталей, элементов и узлов различных конструкций, а также при изготовлении сварных конструкций взамен литых, для исправления пороков литья, восстановления поломанных и изношенных деталей и в инструментальном производстве при изготовлении инструмента, сваренного из двух различных марок стали.
Сварка металлов может производиться в пластическом состоянии (под давлением) или при затвердевании из жидкого состояния (плавлением без давления).
Сварка в пластическом состоянии производится в два приема: вначале части нагревают до сварочного жара, затем давлением или силой удара деформируют свариваемые части и сваривают их.
При сварке плавлением металлы соединяемых частей в месте сварки нагреваются до плавления и сплавляются, образуя прочный шов. Этот способ паиболеее распространен, так как он производительный, экономически выгодный и дает прочное соединение.
По роду источников тепла для нагрева металла сварка делится на электрическую и химическую, при которой используется энергия химических реакций.
Электрическая сварка может быть дуговой и контактной, а химическая — кузнечной, термитной и газовой.
Кузнечная сварка трудоемкая и малопроизводительная и поэтому заменяется более производительным способом сварки — электрической и химической (термитной или газовой).
Электрическая сварка. Электрическая сварка изобретена русским ученым академиком В. В. Петровым в 1802 году. В последующие годы русские ученые Н. Н. Бенардос, Н. Г. Славянов и другие развили и усовершенствовали изобретение В. В. Петрова, благодаря чему электрическая сварка получила широкое распространение как способ прочного и быстрого соединения металлических частей.
Самый распространенный способ электрической сварки — электродуговая сварка металлическим электродом по способу Славянова.
Электродуговой сваркой можно сваривать сталь, чугун серый и ковкий, литье и твердые сплавы, медь, алюминий и его сплавы и т. д.
Ручная электродуговая сварка. При электродуговой сварке электродом служит металлическая проволока. Электрическая дуга, образуемая между электродом и основным металлом, плавит основной металл и электрод, получается общая масса металла в зоне сварки, которая при остывании прочно соединяет свариваемые части. Электрод является одновременно и присадочным материалом.
Электродная проволока выпускается диаметром от 1 до 10 мм. Для сварки углеродистой стали применяют мягкую стальную проволоку с содержанием углерода 0,1 — 0,18% - Для сварки легированных сталей применяют проволоку марок Св.10ГС, Св.10ГСМ, Св. 20 ХГСА и др.
При ручной сварке пользуются электродами — обмазанными специальным составом. Применяют также и голые (непокрытые) электроды, однако качество шва при этом получается менее прочным.
Во всех случаях, когда шов должен быть прочным, применяют только покрытые электроды (фиг. 117).
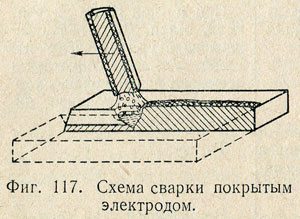
Основными видами пороков электросварки являются: а) непровар — местное отсутствие сплавления между проваренным и основным металлом; б) пористость металла швов; в) шлаковые включения; г) трещины.
Эти пороки появляются вследствие неправильной технологии сварки, применения несоответствующих электродов и других причин. Качество сварного шва также зависит от правильного выбора электрического тока и диаметра электрода.
Кроме указанного способа электросварки, применяется электросварка в струе водорода, который хорошо защищает расплавленный металл от окисления и создает шов лучшего качества и более прочный, чем при обычной электросварке. Благодаря высокой температуре атомноводородного пламени (3000°С) этот способ позволяет сваривать специальные стали сложного химического состава без существенного
изменения химического состава свариваемого шва при хорошей плотности и чистой поверхности его.
Однако широкого распространения этот способ не имеет ввиду сложности его, высокой стоимости специальных вольфрамовых электродов и опасности работы токами повышенного напряжения.
Сварные соединения имеют несколько видов (фиг. 118). Бортовое соединение применяется при толщине листа до 2 мм. Высоту бортов берут равной двойной толщине листа. Шов образуется без присадочного материала.
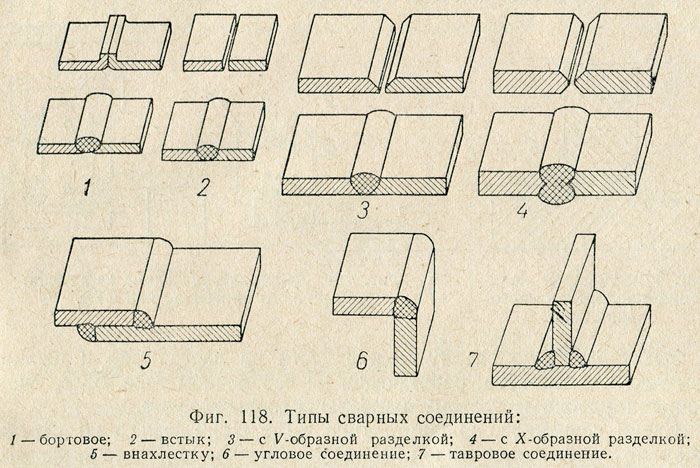
Стыковое соединение без скосов применяется для односторонней сварки деталей толщиной до 6 мм и двусторонней сварки деталей толщиной до 8 мм. Между соединяемыми частями оставляют зазор 1 — 2 мм, который обеспечивает хороший провар основного металла.
V-образное стыковое соединение со скосами применяется для сварки деталей толщиной 6—20 мм.
При большей толщине изделий применяют X-образное соединение.
Соединение внахлестку применяется для деталей толщиной не более 12 мм. Величина перекрытия свариваемого листа берется равной 3 — 5-кратной толщине свариваемого листа.
Угловое соединение делают с наружным расположением шва, для увеличения прочности шов делают выпуклым.
Тавровое соединение может выполняться без скоса кромок и со скосами при сварке ответственных конструкций.
Сварочные швы бывают однослойными и многослойными (фиг. 119).
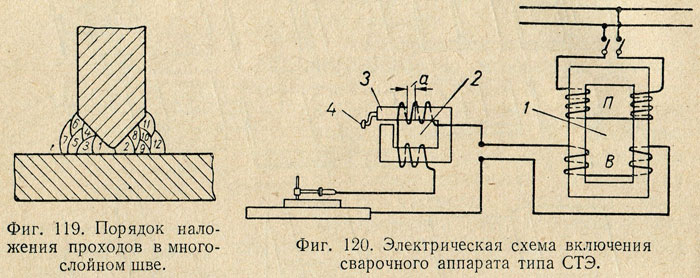
При массовом производстве широко применяется метод автоматической электродуговой сварки, разработанный Институтом электросварки АН УССР. Этот метод резко повышает производительность сварки и улучшает качество сварного шва.
Электродуговую сварку можно вести на постоянном и переменном токе. Аппаратура, работающая на переменном токе, более экономична и удобна и поэтому наиболее распространена.
Схема сварочного аппарата типа СТЭ, работающего на переменном токе от сети напряжением 127 — 220, 380, 500 в, показана на фиг. 120.
Первичная обмотка П трансформатора 1 подключается к сети, к вторичной обмотке В низкого напряжения (55 — 65 в) подключается регулятор тока 2 (реактор), регулирующий ток в сварочной цепи путем изменения индуктивного сопротивления реактора.
Это осуществляется сердечником 3, который может частично перемещаться с помощью винта при вращении рукоятки 4, благодаря чему будет изменяться воздушный зазор а и, следовательно, индуктивность обмотки реактора.
При увеличении зазора магнитное сопротивление сердечника возрастает, индуктивность реактора уменьшается и сварочный ток увеличивается; при уменьшении зазора сварочный ток уменьшается.
предыдущая страница | Содержание | следующая страница |