На главную
3. СПЕЦИАЛЬНЫЕ КОНСТРУКЦИОННЫЕ СТАЛИ
Углеродистая сталь имеет широкое применение, однако во многих случаях инструментального производства, приборостроения и машиностроения она не может быть применена, так как обладает вполне ограниченными свойствами, во многих случаях не удовлетворяющими требованиям эксплуатации того или иного изделия.
Углеродистая сталь обладает сравнительно невысокой прочностью, которая не во всех случаях может быть повышена путем термической обработки, так как эта сталь не обладает глубокой прокаливаемостью (сквозную прокаливаемость можно получить в стержне сечением не более 15 — 18 мм), а, будучи полностью закалена с твердостью Rc = 60 — 64 (мартенситная структура), легко теряет эту твердость (изменяется структура) при нагреве свыше 200 — 220° С.
Углеродистая сталь также не устойчива против кислот и различных окисляющих сред, не жаростойка и не обладает рядом других специальных свойств, которые могут быть достигнуты только прибавкой в сталь, специальных примесей.
Специальные примеси вводятся в сталь для придания ей определенных свойств. К таким примесям относятся: хром, никель, молибден, вольфрам, ванадий, титан, кобальт и др.
Если в стали нет специальных примесей, но имеется в наличии кремния более 0,5% или марганца более 1%, т. е. в количестве большем, чем это необходимо для металлургического производства стали, то эти примеси придают стали специальные свойства и последняя относится к группе легированных сталей.
Все легирующие элементы (за исключением марганца) препятствуют росту зерна стали как при остывании из жидкого состояния, так и при нагреве в твердом состоянии (ковка, термическая обработка). Особенно сильно препятствуют росту зерна хром, молибден, вольфрам, ванадий и титан.
Все легирующие элементы, за исключением кобальта, снижают скорость закалки, т. е. позволяют производить закалку в мягких средах (масло, воздух), и способствуют увеличению глубины прокаливаемости стали.
В сталях, содержащих несколько легирующих элементов, прокаливаемость намного глубже, чем при наличии одного элемента. Глубокая прокаливаемость наблюдается в сталях, содержащих хром и никель, еще более глубокая прокаливаемость — в стали, содержащей хром, никель и вольфрам.
Большинство легирующих элементов препятствует распаду структуры мартенсита при нагреве, т. е. препятствует снижению твердости стали после закалки при последующем нагреве (отпуск, нагрев в эксплуатации). Следовательно, для получения одной и той же твердости после отпуска в углеродистой и легированной стали необходимо последнюю нагреть до более высокой температуры, так как при более высокой температуре отпуска сталь получается более вязкой. Эта вязкость увеличивается еще и оттого, что все легирующие элементы (за исключением марганца) измельчают зерно стали и этим резко увеличивают сопротивление стали ударным нагрузкам.
Особенно сильно измельчают зерно титан, вольфрам, молибден. Поэтому многие марки конструкционных легированных сталей содержат около 0,1% молибдена или титана.
Многие легирующие элементы частично химически соединяются с отдельными элементами стали, а частично растворяются в железе. Такие элементы, как никель, кремний и другие, полностью растворяются в железе и этим резко улучшают механические свойства стали даже без применения термической обработки (закалки).
В углеродистой стали с изменением содержания углерода изменяются и свойства стали — с увеличением углерода снижается вязкость стали, но увеличивается твердость, прокаливаемость, прочность до определенного предела и др.
Еще в большей степени изменяются свойства стали с изменением процентного содержания того или иного легирующего элемента. На этом принципе и основано металлургическое производство многих видов марок специальных сталей и сталей особого назначения, в полной мере обеспечивающих многообразные требования производства к металлическим сплавам.
Конструкционные стали делятся на цементуемые, содержащие углерода 0,1 — 0,22%, и на улучшаемые, содержащие углерода 0,25 — 0,55%.
Стали цементуемые применяются для деталей, работающих на трение и другие механические напряжения. В этом случае сталь подвергается цементации, закалке и низкотемпературному отпуску.
Конструкционные стали применяются для деталей, изготовляемых штамповкой, отбортовкой, загибом в холодном состоянии. В случаях, когда требуется штамповка с глубокой вытяжкой (материал должен быть особо пластичен), применяют низкоуглеродистую сталь (с содержанием углерода 0,08 — 0,15%) с минимальным содержанием кремния (не более 0,05%).
Низкоуглеродистые стали с содержанием углерода от 0,08 до 0,35%, но с повышенным содержанием серы (0,08 — 0,15%) и фосфора (0,08 — 0,15%), применяются как автоматные стали при обработке на станках-автоматах. Повышенное содержание серы и фосфора обеспечивает хорошую обрабатываемость резанием, получается гладкая поверхность и чистая нарезка резьбы. Однако для деталей, подвергающихся ударным нагрузкам, такую сталь применять не рекомендуется, так как повышенное содержание фосфора придает стали холодноломкость.
Механические свойства низкоуглеродистой стали можно улучшить повышенным содержанием марганца до 1,2 — 1,6%. Такая сталь применяется для сварных и штамповочных нецементуемых деталей. Для цементуемых деталей при повышенной нагрузке применяют малоуглеродистую сталь с примесью хрома.
Более высокими механическими свойствами обладает хромоникелевая сталь. Для особо ответственных цементуемых деталей (поршневые пальцы авиадвигателей и т. п.) применяют хромоникелевые стали с прибавкой вольфрама, молибдена.
Конструкционные нецементуемые стали. Эти стали содержат в себе углерод в пределах от 0,25 до 0,55%.
Сталь, содержащая углерода 0,25 — 0,30%, весьма пластична, но прочность ее невысокая (σ = 40 — 45 кг/мм2). С повышением содержания углерода пластичность понижается, а прочность увеличивается и для стали марок 40 — 50 достигает σ = 50 кг/мм2. Поэтому в тех случаях, когда требуются высокие пластические свойства, необходимо применять сталь с более низким содержанием углерода.
Углеродистую сталь, из которой изготовляются детали, работающие с большой нагрузкой, подвергают термической обработке или заменяют ее легированной сталью.
В результате термообработки сопротивление стали разрывающим, ударным и крутящим усилиям резко повышается.
В машиностроении сталь марки 25 применяют для мелких деталей — шайб, винтов и т. д. Из стали 35 изготовляют болты, гайки и другие мелкие детали без применения термообработки. Сталь 45 применяют для изготовления рычагов, корпусов и других неответственных деталей с последующей закалкой и отпуском или без применения термообработки.
В тех случаях, когда механические свойства углеродистой стали не удовлетворяют требованиям, применяют легированные стали. Наиболее частое применение имеют легированные стали, содержащие хром, который резко улучшает механические свойства стали, в особенности после термической обработки.
Для ответственных деталей, претерпевающих большие напряжения в эксплуатации, применяют хромоникелевые стали.
В зависимости от свойств стали объединяются в следующие группы:
1. Конструкционная сталь, идущая на изготовление деталей машин. Эта группа сталей подразделяется на стали цементуемые и стали улучшаемые.
2. Инструментальные стали, идущие на изготовление различного вида инструмента. Эта группа подразделяется на низколегированные и высоколегированные инструментальные стали, а также на стали для изготовления штампов и быстрорежущие стали.
3. Стали особого назначения. К ним относятся стали, обладающие каким-нибудь резко выраженным свойством. Такими сталями являются: нержавеющие, жароупорные и теплоустойчивые, износоустойчивые, с особыми свойствами теплового расширения, с особыми магнитными и электрическими свойствами и т. д.
Характеристика и примерное назначение некоторых марок сталей приводятся в табл. 33.
Таблица 33
Харакиеристика и примерное назначение некоторых марок углеродистых и легированных сталей
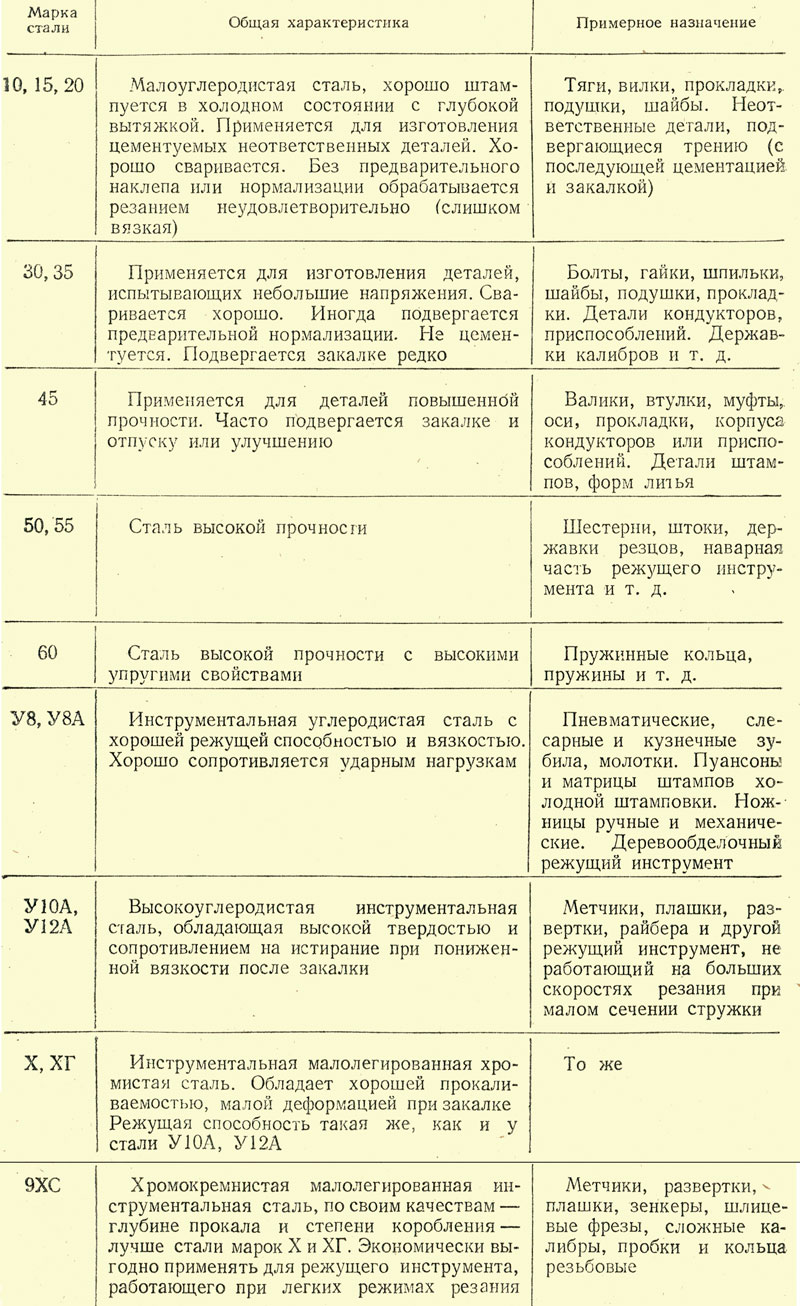
Маркировка легированных сталей. В целях упрощения клеймления прутков легированных сталей ГОСТ предусматривает сокращенную маркировку, в которой легирующие элементы обозначены буквами, а цифры показывают содержание углерода или легирующих элементов. Первые две цифры показывают среднее содержание углерода в сотых долях процента. Цифры, идущие после буквы, указывают содержание (среднее) легирующего элемента в целых процентах.
Если содержание легирующего элемента меньше или около 1%, то цифра после буквы отсутствует, если содержание около 1,5%, то ставится цифра 1, если около 2% — цифра 2 и т. д.
Легирующие элементы обозначаются буквами: никель — Ni, вольфрам — W, фосфор — Р, хром — Сг, ванадий — V, титан — Ti, кобальт — Со, молибден — Мо, медь — Си, кремний — Si, марганец — Мn, алюминий — Аl.
Для того чтобы показать, что сталь чистая по сере и фосфору (S ≤ 0,03%; Р ≤ 0,03%), а также соблюдены все технические условия высококачественной стали, в конце обозначения ставят букву А.
При наличии в стали многих легирующих элементов для упрощения наносят сокращенную маркировку, пропуская некоторые элементы.
Некоторые высоколегированные стали выделены в отдельные группы. Каждой группе присвоена своя буква, которая идет первой в марочном обозначении: хромистые нержавеющие стали — Ж, хромоникелевые нержавеющие стали — Я, магнитные стали — Е, быстрорежущие стали — Р, шарикоподшипниковые стали — Ш.
В инструментальных сталях в маркировке не указывается содержание углерода, т. е. обозначение марки начинается не с цифр, а с букв, например: сталь состава 1,45 — 1,70% С; 11 — 12,5% Сr и 0,5 — 0,8 Mо обозначается Х12М.
Стали, выплавленные на заводе «Электросталь», помимо стандартного обозначения имеют еще в начале марки букву Э (ЭХ12М и т. д.), которая показывает только то, что сталь была выплавлена на заводе «Электросталь».
Нестандартные стали обозначаются самым разнообразным образом. Например, опытные марки, выплавленные на заводе «Электросталь», обозначаются буквой И (исследовательские) и порядковым номером, например: сталь ЭИ179 и др.
предыдущая страница | Содержание | следующая страница |