На главную
4. ИНСТРУМЕНТАЛЬНЫЕ СТАЛИ
Все инструментальные стали делятся на четыре категории: а) углеродистые инструментальные стали; б) легированные инструментальные стали; в) штамповые стали; г) быстрорежущие стали.
Углеродистые инструментальные стали. Все углеродистые стали содержат марганца в пределах 0,15 — 0,35%; кремния не более 0,30%; серы не более 0,020% и фосфора не более 0,030%.
По содержанию углерода эти стали делятся на марки: У7А — содержит 0,6 — 0,74% С; У8А — 0,75 — 0,84% С; У9А — 0,86 — 0,94% С; У10А — 0,95 — 1,09%С; У12А — 1,25% С и У13А — 1,26 — 1,40% С.
Свойства и применение углеродистых инструментальных сталей, а также режимы горячей и термической обработки зависят главным образом от содержания углерода в стали.
Сталь У7А применяется для инструмента, подвергающегося ударам и толчкам, требующего вязкости при умеренной твердости, например: для зубил, кузнечных штампов, кузнечного инструмента и т. п.
Сталь У8А применяется для инструмента, подвергающегося ударам, требующего хорошей вязкости при высокой твердости, например: матрицы, пуансоны для холодной штамповки, ножницы и ножи по металлу и дереву, столярный инструмент, пневматический инструмент и т. д.
Сталь У10А применяется для инструмента, не подвергающегося сильным ударам, при максимальной твердости на режущей грани, например: металлорежущий инструмент — метчики, развертки, сверла, фрезы; мерительный стержневой инструмент и т. д.
Сталь У12А применяется для инструмента с максимальной износоустойчивостью при наивысшей твердости, например: напильники, зубила для насечки напильников, граверный инструмент, волочильные доски, калибры-пробки гладкие и резьбовые и т. д.
Легированные инструментальные стали. Хромистые стали применяются для режущего и мерительного инструмента. Хром способствует углублению прокаливаемости и частично повышает устойчивость стали против отпуска. Кроме этого, хром частично растворяется в цементите и делает его более твердым, а сталь более устойчивой против износа.
Для режущего и мерительного инструмента применяют стали с содержанием углерода около 1% и хрома около 1,5%. Закалка такой стали производится в масле. Введение в хромистую сталь около 1% кремния еще в большей степени улучшает свойства стали. Такая сталь марки 9ХС легко закаливается в масле на полную глубину с минимальной деформацией. Недостатком стали 9ХС является повышенная склонность к обезуглероживанию и плохая обрабатываемость по сравнению с углеродистой сталью. Эта сталь рекомендуется для такого инструмента, как развертки, метчики, плашки, калибры, пробки гладкие и т. д. Для инструмента, требующего минимальной деформации при закалке, рекомендуется применять хромомарганцовистые стали.
Хром и марганец снижают критическую скорость закалки и степень деформации при закалке.
К малодеформирующим сталям можно отнести стали: хромокремнистую 9XG, хромистую ХГ и особенно хромовольфрамовую ХВГ.
Эти марки стали применяются для режущего инструмента, сложного мерительного и частично для штампов холодной штамповки (сталь ХВГ — для матриц и пуансонов малых габаритов).
В тех случаях, когда требуется изготовить высокой стойкости режущий инструмент (протяжки, сложные фрезы) с минимальной деформацией при закалке или штамп сложной конфигурации, не допускающий деформации при закалке, применяют высокохромистую сталь Х12 с содержанием хрома до 13%, а еще лучше — Х12М с прибавкой вольфрама и молибдена в незначительном количестве.
Когда требуется изготовить режущий инструмент с высокой стойкостью режущей кромки для обработки твердых материалов на небольших скоростях (граверные резцы и резчики, резцы для чистовой обработки твердых металлов и т. д.), а также различные клейма сложной конфигурации, рекомендуется применять так называемую алмазную сталь марки ХВ5 с содержанием углерода до 1,5%, хрома до 7% и вольфрама до 5,5%.
Сталь, идущая для изготовления штампов, работающих при высоких давлениях, должна иметь высокий предел текучести (пропорциональности). Для кузнечных штампов важно иметь хорошую вязкость металла, чтобы штамп не разрушился во время работы от ударов. Для штампов, работающих в легких условиях, применяют углеродистую сталь марок У7А, У8А и реже У10А. Для штампов, работающих в тяжелых условиях, применяют легированные стали.
Для кузнечных (молотовых) штампов применяют стали с небольшим содержанием углерода и легирующих элементов (хрома, никеля, марганца, молибдена). Наиболее часто применяются для этих штампов марки стали 5ХГМ, 5ХНТ.
Для чеканочных штампов наилучшие результаты по стойкости имеет сталь ЗХ2В8, но так как она содержит много остродефицитного элемента вольфрама, то ее следует заменять сталью марки 7X3.
Для пневматического инструмента применяют хромокремнистую сталь марки 4ХС. Для форм литья под давлением рекомендуется применять сталь марки ЗХ2В8 или ее заменитель 7X3. Для прессформ следует применять стали марок 5ХНТ, 5ХНВ и 4ХВС.
Выбор марки стали для штампа, формы литья или прессформы полностью еще не определяет стойкости инструмента, так как существенную роль играет правильно выбранный технологический процесс ковки и термической обработки.
При ковке заготовок матриц или пуансонов, а также для деталей форм литья под давлением весьма важно выдержать температурный режим ковки. Не менее важен правильный режим отжига заготовки после поковки. При обработке детали штампа или формы литья перед закалкой слесарь, изготовляющий штамп, должен учитывать возможную деформацию детали при закалке и производить обработку детали так, чтобы можно было после закалки довести ее до окончательных размеров и требуемого класса чистоты с минимальной затратой времени.
Если матрица, пуансон или деталь формы имеют места, трудно обрабатываемые в закаленном виде шлифовкой на станке (углубления сложной формы, прорези, щели и т. д.), то эти места необходимо обрабатывать до закалки почти до окончательных размеров (оставляя припуск в несколько микрон), чтобы после закалки ограничиться только зачисткой мелкозернистой наждачной шкуркой.
Быстрорежущие стали. Инструментальная углеродистая закаленная сталь при нагреве свыше 200° С начинает резко терять свою твердость, в результате чего стойкость режущей кромки инструмента быстро снижается, кромка изнашивается (садится).
Твердость быстрорежущей закаленной стали снижается при нагреве до 600 — 650° С.
Режущий инструмент из углеродистой стали может иметь после закалки твердость выше твердости режущего инструмента из быстрорежущей стали, однако инструмент из углеродистой стали может работать только при условии, когда режущая кромка его не будет нагреваться выше 200° С, т. е. когда снимается мало металлической стружки и не выделяется много тепла при резании.
Режущий инструмент, изготовленный из быстрорежущей стали, будучи стоек при повышенных температурах, может работать на больших скоростях и снимать больший объем стружки, в единицу времени. Красностойкость быстрорежущей стали объясняется тем, что специальные элементы, входящие в состав стали, препятствуют распаду структуры мартенсита. Такими элементами являются: хром, вольфрам, молибден и ванадий. Эти элементы, образуя карбиды с углеродом, препятствуют распаду мартенсита, так как они выделяются (выпадают) из мартенсита при более высокой температуре, чем выделяется углерод из мартенсита в углеродистых сталях.
Наибольшее распространение имеет быстрорежущая сталь марки Р18 и Р9.
Сталь Р18 менее чувствительна к перегреву, в ней нет заметного роста зерна даже при длительной выдержке при температуре 1250 — 1280° С, тогда как сталь Р9 весьма чувствительна к перегреву и требует строгого температурного нагрева при ковке и закалке.
Обычно после закалки твердость стали Р18 Rc = 54 — 56. Последующим отпуском при 560 — 580° твердость стали повышается.
Повторным двух - и трехкратным отпуском можно повысить твердость до Rc = 62 — 64. Выдержка при каждом отпуске устанавливается 60 — 70 мин.
Еще в большей степени можно повысить твердость и стойкость стали Р18 и Р9 обработкой холодом после повторных отпусков, которая широко внедрена в термическую обработку стали в настоящее время.
В целях увеличения стойкости режущего инструмента из быстрорежущей стали получило широкое распространение цианирование закаленного и многократно отпущенного инструмента.
При закалке быстрорежущей стали и вообще высоколегированной стали необходимо придерживаться особого режима, так как эти стали имеют более пониженную теплопроводность, чем обычные углеродистые или малолегированные стали, и склонны к термическим напряжениям при быстром нагреве. Поэтому быстрорежущая сталь при нагреве под закалку должна предварительно подогреваться в отдельной печи или соляной ванне до температуры 600 — 650° и затем окончательно нагреваться до закалочной температуры 1250 — 1280° С. В том случае, когда закалке подвергается инструмент больших размеров или сложной конфигурации, необходимо делать двойной предварительный подогрев на 600 — 650° С, затем на 850 — 900° С и после этого нагревать его до закалочной температуры. Скорость нагрева необходимо также выдерживать.
Рекомендуется такая скорость нагрева на 1 мм диаметра или сечения инструмента из стали Р18:
Для нагрева в печи до 650°С — 60 сек.
Для нагрева в печи до 850°С — 30 сек.
Для нагрева в соляной ванне до 1200 — 1300°С — 6 — 7 сек.
Для нагрева в печи до 1200 — 1300°С — 10 — 12 сек.
В том случае, когда инструмент больших размеров и сложной формы, рекомендуется производить ступенчатую закалку: первичное охлаждение в расплавленной соли (азотнокислый калий: — KNO3) при температуре около 500° С и после непродолжительной выдержки — закалка в масле или на воздухе. Этим снижается вероятность появления термических напряжений и коробления. Отпуск следует производить сейчас же после закалки.
В табл. 34 и 35 приведены химический состав и условия термической обработки инструментальных сталей.
Таблица 34
Химический состав, температура закалки и отпуска сталей для штампов и инструмента, предназначенного для штамповки и резки металлов в холодном состоянии
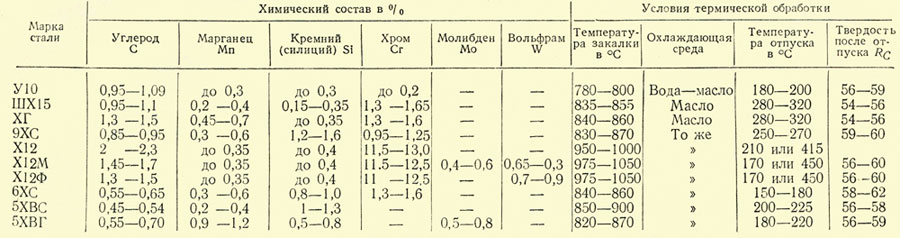
Таблица 35
Химический состав, температура закалки и отпуска сталей для режущего и инструмента
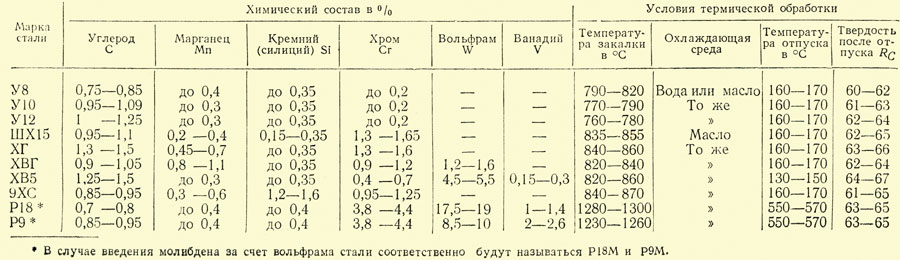
предыдущая страница | Содержание | следующая страница |