На главную
§ 79. ВЫБОР РЕЖИМА РЕЗАНИЯ
Для правильного назначения скорости резания по выбранным материалу, геометрическим параметрам и диаметру фрезы в соответствии с выбранной подачей на один зуб следует принять наиболее рациональную стойкость фрезы, соответствующую нормальному затуплению (износу), и применять соответствующее охлаждение фрезы.
Период стойкости фрезы
В процессе работы фреза затупляется. Затупление фрезы происходит вследствие износа, вызванного трением задней поверхности зуба фрезы об обработанную поверхность и трением сходящей стружки о переднюю поверхность зуба.
Износ фрез в зависимости от условий резания происходит или по задней поверхности, когда толщина срезаемого слоя анаиб меньше 0,08 мм или одновременно по задней и передней поверхностям при резании с толщиной срезаемого слоя анаиб больше 0,08 мм.
Цилиндрические, дисковые, концевые, фасонные и прорезные фрезы, работающие в зоне тонких стружек, изнашиваются в основном по задней поверхности.
Признаки начала затупления фрезы — появление вибраций, неровная (рваная) поверхность обработки и чрезмерный нагрев фрезы вследствие увеличения трения.
Исходя из допускаемого износа режущей части инструмента, устанавливают период стойкости фрезы, т. е. длительность непрерывной работы ее от заточки до заточки при нормальном затуплении. Период стойкости обозначают Т и измеряют в минутах непрерывной (машинной) работы фрезы. Чем выше скорость резания, тем скорее тупится фреза и, следовательно, период стойкости ее уменьшается. Наоборот, чем меньше скорость резания, тем дольше фреза будет работать без переточки и, следовательно, иметь больший период стойкости. При этом период стойкости фрезы значительно изменяется при незначительном даже изменении скорости резания. Так, при обработке конструкционной стали с σ = 75 кГ/мм2 твердосплавной торцовой фрезой увеличение скорости резания на 15% вызывает уменьшение периода стойкости вдвое, а уменьшение скорости резания на 20% вызывает увеличение периода стойкости втрое.
При работе на больших скоростях производительность труда получается более высокой, техническая норма технологического времени меньшей и, следовательно, штучный расценок ниже. Но при этом вследствие уменьшения периода стойкости фрезу приходится значительно чаще затачивать, затрачивая время на ее съем и установку, что в свою очередь вызывает увеличение вспомогательного времени. Кроме того, с каждой переточкой срок службы фрезы сокращается, а это вместе со стоимостью заточки увеличивает стоимость обработки. Может случиться, что выигрыш на увеличение производительности в результате высокой скорости резания окажется меньше, чем повышенные расходы на более частую переточку фрезы.
С другой стороны, при работе на малых скоростях резания производительность труда получается низкой, что вызывает увеличение доли технологического времени в штучной норме и, следовательно, увеличение расценка. При этом экономия на увеличение периода стойкости фрезы и более редкой ее заточке может оказаться меньше, чем потери на производительности от заниженной скорости резания.
Таким образом, рациональная скорость резания находится где-то между завышенной и заниженной, соответствуя тому периоду стойкости фрезы, при котором стоимость переточки соответствует выигрышу в производительности. Стойкость, соответствующая наиболее рациональной скорости резания, называется экономической стойкостью.
В табл. 48 приведены средние периоды стойкости фрез, соответствующие ее экономической стойкости, в зависимости от типа фрезы, обрабатываемого материала, марки режущей части инструмента и характера обработки.
Периоды стойкости фрез, указанных в табл. 48, рассчитаны на одноинструментную обработку, т. е. на работу одной фрезы. В случае работы набором фрез или одновременной работы нескольких шпинделей с подобранным комплектом фрез — так называемой многоинструментной обработки — период стойкости всей наладки должен быть большим, чем для одноинструментной обработки, так как затраты времени на съем, заточку и установку вновь большого количества фрез значительно превышают принятые при определении экономической стойкости одной фрезы.
Для установления периода стойкости при многоинструментной обработке применяют следующую формулу:
Т = К (Т1 + Т2 + ... + Тi ) мин.
,где Т1, T2; T3,..., Тi — периоды стойкости первой, второй и т. д. до последней фрезы данного набора или комплекта;
К — коэффициент, учитывающий количество фрез в наборе или комплекте; значения К даны ниже.

Таблица 48
Средние периоды стойкости фрез T в минутах
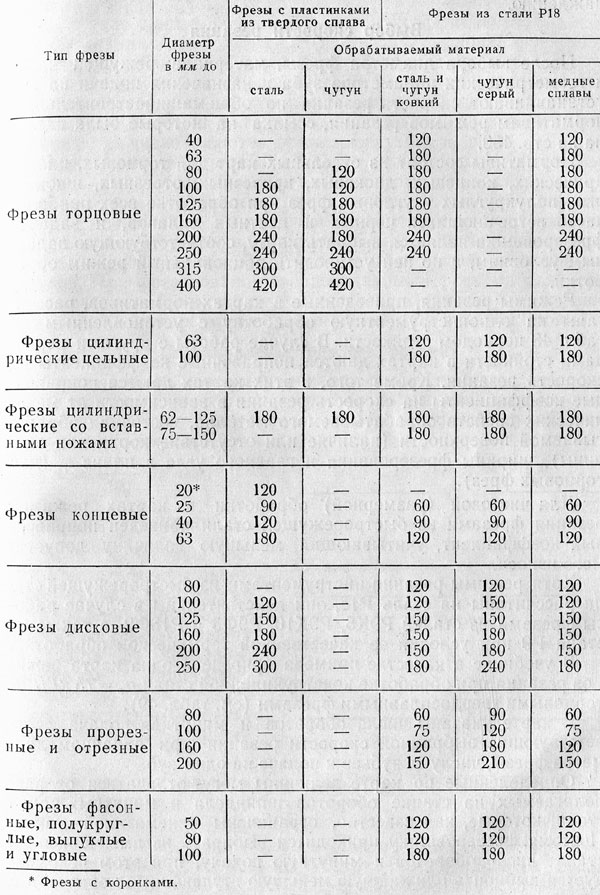
Чтобы уменьшить нагревание фрезы при резании и уменьшить износ из-за размягчения режущей кромки, прибегают к охлаждению.
Выбор скорости резания
После выбора диаметра фрезы, материала режущей части и геометрических параметров зуба и назначения подачи на зуб устанавливают скорость резания по общемашиностроительным нормативам режимов резания.
Нормативы состоят из отдельных карт для торцовых, цилиндрических, концевых, дисковых, прорезных, отрезных, шпоночных, полукруглых и угловых фрез при обработке всех наиболее часто встречающихся черных и цветных сплавов, и задачей фрезеровщика является выбрать карту, соответствующую заданным условиям, и по ней установить рациональный режим обработки.
Режимы резания, приведенные в картах нормативов, рассчитаны на одноинструментную обработку с установленным по табл. 48 периодом стойкости. В случае работы с другими периодами стойкости в картах даются поправочные коэффициенты на скорость резания. Кроме того, в этих картах даются поправочные коэффициенты на скорость резания в зависимости от механических свойств обрабатываемого металла, состояния обрабатываемой поверхности (наличие или отсутствие корки или окалины), ширины фрезерования и главного угла в плане φ (для торцовых фрез).
Для чистовой (размерной) обработки в картах режимов резания фрезами из быстрорежущей стали приведен поправочный коэффициент, учитывающий меньшую величину допустимого износа.
Хотя режимы резания инструментами из быстрорежущей стали рассчитаны на сталь Р18, они действительны в случае работы фрезами из сталей Р9К5, Р9К10, Р9Ф5 и Р18Ф2, а также из стали Р9 при условии ее качественной термической обработки.
В учебнике в качестве примера приведена одна карта режимов резания при обработке конструкционной стали σв = 75 кГ/мм2 торцовыми твердосплавными фрезами (см. табл. 49).
В карте указаны числа оборотов и минутная подача, соответствующие выбранной скорости резания при заданном диаметре фрезы, числу ее зубьев и подаче на один зуб.
Определенные по карте величины могут отличаться от располагаемых на станке оборотов шпинделя и минутных подач стола, которые, как известно, ограничены кинематикой станка. Поэтому фрезеровщику приходится выбирать из имеющихся на станке число оборотов и минутную подачу; при этом рекомендуется выбирать ближайшую меньшую ступень чисел оборотов и подач, чтобы фактически осуществленные режимы резания не превышали выбранных по карте во избежание преждевременного затупления фрезы.
В случае применения поправочных коэффициентов на скорость резания в зависимости от измененных условий фрезерования против принятых в карте (другой период стойкости, другие механические свойства обрабатываемого металла, состояние поверхности заготовки, другая ширина фрезерования, другой угол в плане φ, черновая или чистовая обработка) соответственно изменяются число оборотов фрезы и минутная подача.
Как показала практика эксплуатации консольно-фрезерных станков, при работе фрезами из быстрорежущей стали иногда при некотором соотношении параметров режима резания возникают вибрации. В этих случаях рекомендуется увеличить подачу на одну ступень или применить фрезы с неравномерным шагом по конструкции В. Я. Карасева и крутой винтовой канавкой. При фрезеровании твердосплавными фрезами для борьбы с вибрацией рекомендуется ставить маховики на оправку и делать у сборных фрез неравномерный шаг вставных ножей.
Установление режима резания
После выбора и корректирования по фактическим (паспортным) данным станка числа оборотов и минутной подачи устанавливают фактическую скорость резания и фактическую подачу по известным формулам:
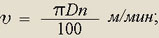

Если выбранный режим не отвечает мощности станка, необходимо установленную по нормативам минутную подачу s снизить до величины, допускаемой мощностью электродвигателя станка, и соответственно снизить число оборотов шпинделя.
Пример выбора режима резания
Рассмотрим на конкретном примере порядок выбора режима резания при фрезеровании заготовки (рис. 331) из проката 60 X 70 x 900 мм стали 45 с σb = 65 кГ/мм2 на вертикально-фрезерном станке 6М12П.
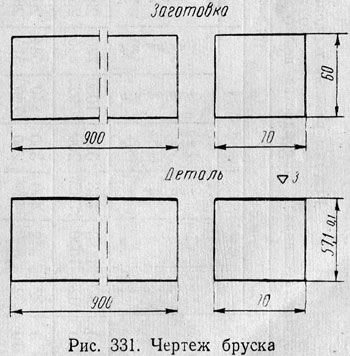
Таблица 49
Режимы резания торцовыми фрезами с пластинами Т15К6
Сталь конструкционная углеродистая и легированная хромистая и хромоникелевая с σb = 75 кГ/мм2
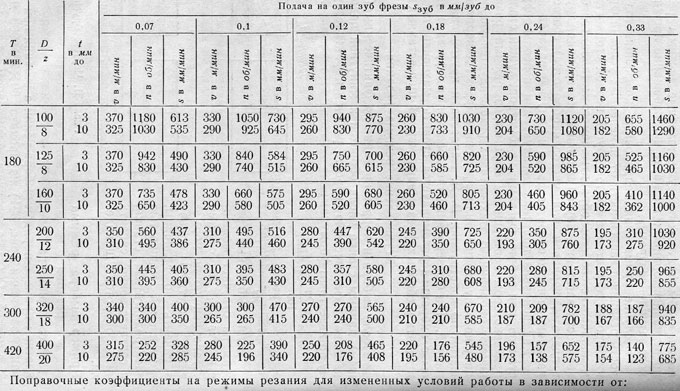
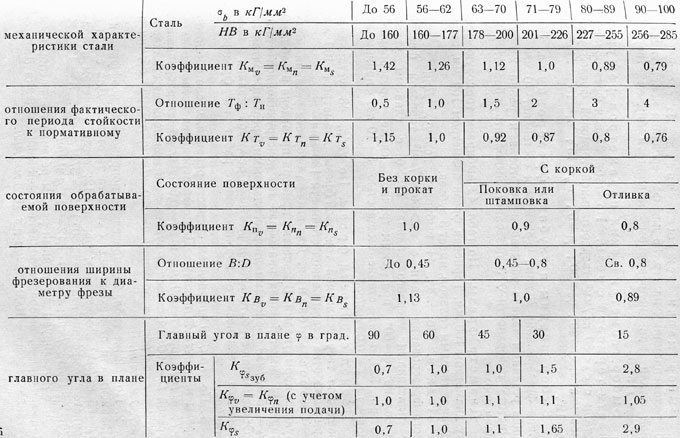
Выбор марки режущей части. В соответствии с рекомендациями на стр. 56 для фрезерования конструкционной стали при непрерывном резании выбираем твердый сплав Т15К6.
Выбор геометрических параметров режущей части торцовой фрезы. По табл. 37 для фрезерования стали с σb меньше 80 кГ/мм2 твердосплавной торцовой фрезой устанавливаем: φ = 60°; φ0 = 30°; φ1 = 5°; αn = 15°; α1 = 15°; γ = - 5°; λ = 12°.
Выбор ширины и глубины фрезерования. Ширина фрезерования В дана чертежом и составляет 70 мм; глубина резания t задана размерами заготовки и равна 2,9 мм. Чистота поверхности 3 позволяет выполнить обработку за один проход.
Диаметр фрезы. По табл. 42 выбираем торцовую фрезу диаметром 100 мм. Торцовая фреза диаметром 100 мм, оснащенная твердым сплавом, имеет 8 зубьев.
Подача. По табл. 44 выбираем подачу. Для чернового фрезерования стали с σb больше 60 кГ/мм2 торцовой фрезой с пластинами твердого сплава Т15К6 с главным углом в плане φ=60° при симметричной схеме фрезерования по рис. 324, а на станке мощностью 5 — 10 квт принимаем подачу sзу6 =0,09 мм/зуб.
Период стойкости фрезы. По табл. 48 устанавливаем для твердосплавной торцовой фрезы диаметром 100 мм при обработке стали период стойкости 180 мин.
Скорость резания. Для выбора скорости резания пользуются нормативами. В качестве примера приведена в табл. 49 карта режимов резания при обработке конструкционной стали σb = 75 кГ/мм2 торцовыми твердосплавными фрезами, взятая из «Общемашиностроительных нормативов режимов резания и времени для технического нормирования работ на фрезерных станках».
1. По табл. 49 определяем скорость резания, число оборотов фрезы и минутную подачу. Для фрезерования стали с σb = 75 кГ/мм2 при t = 2,9 мм и sz = 0,09 мм/зуб твердосплавной фрезой D = 100 мм с числом зубьев z = 8 при периоде стойкости 180 мин. по таблице получим: v = 330 м/мин; n = 1050 об/мин и s = 730 мм/мин.
2. По той же табл. 49 определяем поправочный коэффициент в зависимости от механических свойств заготовки. Для стали с σb = 65 кГ/мм2 коэффициент равен 1,12; тогда с учетом поправочного коэффициента υ = 330 · 1,12 = 370 м/мин; n = 1050 X 1,12 = 1176 об/мин; s = 730 · 1,12 = 817 мм/мин.
3. Корректируем выбранный режим резания по паспортным данным станка, выбрав ближайшие меньшие значения n и s. Устанавливаем n = 1000 об/мин и s = 630 мм/мин.
После корректировки определяем фактические скорость резания и подачу фрезы:

Sзуб = s : (z · n) = 630 : (8 · 1000) = 0,08 мм/зуб.
Проверка выбранного режима по мощности
1. Подобно подсчету, приведенному в примере 24, определим эффективную мощность Nе, потребную на резание.
Наибольшую толщину срезаемого слоя анаиб определим по формуле (28а):
анаиб = sзуб = 0,08 мм.
Среднее поперечное сечение срезаемого слоя Fсред определим по формуле (35):

Окружную силу резания Р определим по формуле (37):
P = p · Fсред = 350 · 0,4 = 140 кГ,
где удельное давление р определено по табл. 33 как среднее между значениями для стали с σb = 60 кГ/мм2 и σb = 75 кГ/мм2 при толщине срезаемого слоя анаиб = 0,08 мм.
Эффективную мощность Nе определим по формуле (406):

2. Определенное значение потребной мощности Nе проверяем по мощности электродвигателя с учетом к. п. д. станка. При 1000 об/мин согласно паспорту станка 6М12П (см. стр. 448) к. п. д. составляет 0,75. При Nэ = 7 квт и к. п. д. станка η = 0,75 мощность на шпинделе:
Nе = Nэ · η = 7 · 0,75 = 5,25 квт
т. е. меньше мощности, потребной на резание по выбранному режиму.
3. Корректируем минутную подачу, уменьшая ее на 30% в соответствии с расчетной и располагаемой эффективной мощностью, что соответствует s = 630 · 0,7 = 441 мм/мин. Принимаем по паспорту станка ближайшую минутную подачу s = 400 мм/мин. Тогда
Sзуб = s : (n · z) = 400 : (1000 · 8) = 0,05 мм/зуб
и наибольшая толщина срезаемого слоя
aнаиб = 0,05 мм.
При этом удельное давление резания р примем по табл. 33 400 кГ/мм2.
При этом потребная мощность Nе составит:
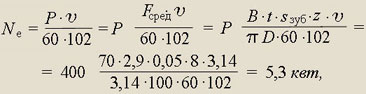
что соответствует располагаемой мощности станка.
4. Проверим на прочность механизм продольной подачи стола.
При Nе = 5,3 квт мощность, затрачиваемая на подачу Nпод, составит 0,15 Nе:
Nпод = 0,15 · 5,3 = 0,8 квт
Усилие подачи Pпод, можно определить по формуле (406), подставив скорость подачи s вместо V.
Тогда из формулы (406) следует:
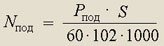
или
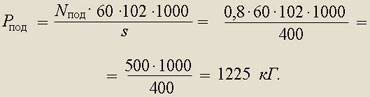
что меньше допустимого по паспорту усилия, равного 1500 кГ.
5. Окончательно выбранный режим резания составит:
V = 314 м/мин; n = 1000 об/мин; s = 400 мм/мин.
6. Проверим по табл. 34 удельную производительность данной обработки.
Минутный объем срезаемого слоя (стружки) по формуле (43):

При мощности электродвигателя Nэ = 7 квт удельная производительность по формуле (45):
ω = W : Nэ = 81 : 7 = 11,5 см3/квт · мин.
По табл. 34 удельная производительность ω при фрезеровании торцовой фрезой конструкционной стали σb = 60 — 70 кГ/мм2 составляет 14 см3/квт · мин.
Таким образом, выбранный режим резания соответствует, требованиям производительного фрезерования.
КОНТРОЛЬНЫЕ ВОПРОСЫ
1. Что называется наивыгоднейшим режимом резания при фрезеровании?
2. От каких факторов зависит выбор режима резания при фрезеровании?
3. Расскажите порядок выбора режима резания?
4. Что называется экономической стойкостью фрезы?
5. Как влияет стойкость фрезы на скорость резания?
6. Выберите по табл. 49 режим резания для черновой обработки бруска из конструкционной стали с σb = 75 кГ/мм2 торцовой фрезой, если ширина В = 60 мм и глубина резания t = 3 мм.
7. Определите потребную мощность Ne для обработки на вертикально-фрезерном станке 6М12П заготовки из проката полосовой конструкционной стали σb = 65 кГ/мм2, шириной В = 70 мм, при глубине резания t = 2,5 мм. Выбранный режим n = 600 об/мин, s = 475 мм/мин; фреза диаметром 160 мм с 10 зубьями из твердого сплава Т15К6.