На главную
4. ШАБРЕНИЕ
Шабрение применяется при изготовлении нового и ремонте старого оборудования, при изготовлении контрольно-поверочных плит, деталей приборов и т. д.
Поверхности, подлежащие шабрению, должны быть предварительно обработаны резцами, фрезами, напильниками или другим режущим инструментом.
Для определения, какую именно часть поверхности необходимо шабрить, деталь пришабриваемой поверхностью кладут на контрольную плиту, покрытую тонким слоем краски, и с легким нажимом перемещают по плите в разных направлениях.
Выступающие места пришабриваемой поверхности покрываются пятнами краски, эти места подлежат соскабливанию (шабрению).
Качество шабрения определяется по прилеганию сопрягаемых поверхностей — по числу точек соприкасания с контрольной плитой (по числу точек на единицу площади).
Принято считать прилегание сопрягаемых поверхностей плотным, если число точек соприкасания на площади 25 X 25 мм будет не менее трех. Для проверки шабруемой поверхности служит специальная рамка (фиг. 65). Накладывая ее на обрабатываемую поверхность, можно легко определить качество шабрения путем подсчета точек, полученных после притирки на контрольной плите. При обработке точных поверхностей число точек на площади рамки (фиг. 65) должно быть не менее 15. Для очень точного шабрения принимают число точек на площади рамки не менее 30.
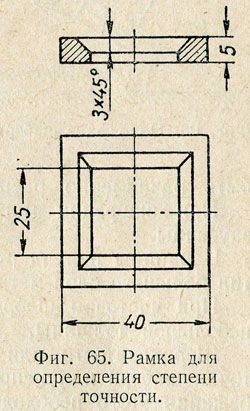
Практически установлено, что припуск на шабрение необходимо оставлять в пределах от 0,1 до 0,4 мм, в зависимости от длины и ширины шабруемой поверхности.
С увеличением габаритов детали, подлежащей шабрению, припуск увеличивается.
При шабрении шабер следует держать под углом 30 — 40° к плоскости шабрения, при этом шабер должен двигаться вперед и назад на расстояние не более 10 — 15 мм в различных направлениях, перекрещивая штрихи под углом 45° (фиг. 66).
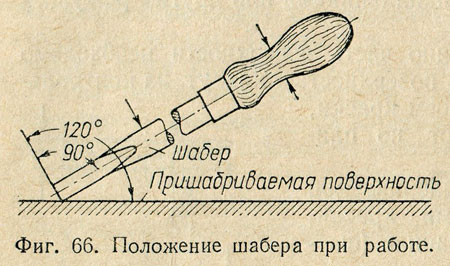
Площадки, образованные штрихами, после шабрения должны иметь вид квадратиков или ромбов.
После снятия шабером покрытых краской мест поверхность детали счищают щеткой и тщательно протирают салфеткой. Затем деталь снова накладывают на контрольную плиту и продолжают шабрение закрашенных мест до тех пор, пока число точек на пришабриваемой детали не достигнет нормы.
При шабрении цилиндрических поверхностей подшипников для валов или шпинделей число точек должно быть не менее 15 на площади рамки.
Для контроля качества шабрения подшипников применяют специальные оправки, валы или шпиндели. Принцип шабрения заключается в том, что вал или оправку, смазанную слоем краски, вкладывают в подшипник, затем поворачивают 3 — 4 раза вокруг своей оси, вынимают и производят шабрение подшипника.
Шабрение подшипника ведут до тех пор, пока не будет достигнута прилегаемость к валу не менее 3/4 всей его поверхности. Пятна краски должны быть равномерно распределены по всей поверхности подшипника.
При шабрении могут появляться царапины, шероховатости и заусенцы.
Царапины получаются при сильном нажиме на шабер, при снятии большого слоя металла с поверхности.
При чистовом шабрении должно производиться снятие стружки небольшой толщины.
Шероховатости или заусенцы получаются от неправильной заточки шабера или неправильного движения им при работе. Для избежания этого необходимо правильно затачивать и заправлять шабер, не работать тупым шабером.
Поверхность деталей, подлежащих обработке шабером, подвергают предварительной проверке контрольными плитами и линейками (фиг. 67). Если прямолинейность пришабриваемой поверхности на длине 1000 мм достигает от 0,5 до 1 мм, то поверхность необходимо исправить фрезерованием, строганием или шлифованием.
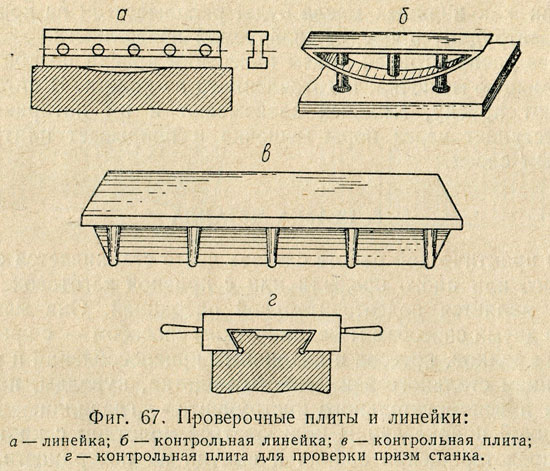
Чтобы предотвратить неточность проверки шабруемой поверхности, следует периодически проверять контрольные плиты и держать их в надлежащей чистоте.
Заточка и заправка шаберов. Заточку шаберов следует производить на корундовом круге зернистостью не крупнее 60 и твердостью СМ1 или СМ2. После заточки на лезвии шабера получаются неровности и заусенцы, лезвие шабера необходимо заправлять на чугунной плите с применением мелкого корундового порошка № 240 или № 320, смешанного с машинным маслом.
При заправке шабера (фиг. 68,а) по радиусу торец его прижимают к вертикальной стенке плитки А, чтобы избежать завалов рабочей грани. После этого производят заправку боковых граней, как показано на фиг. 68,6.
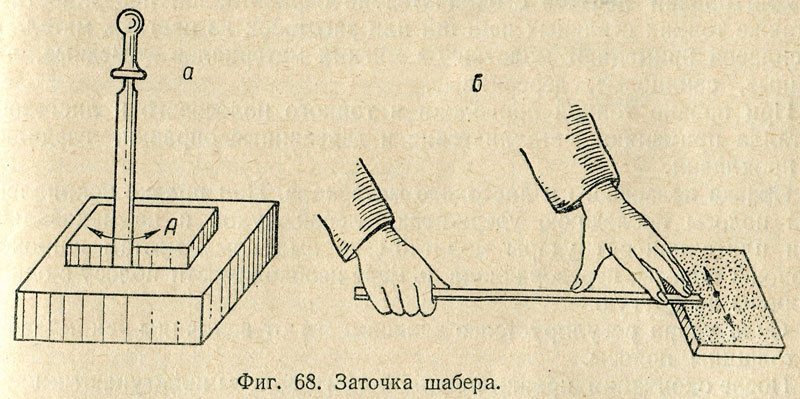
Практикой установлено, что для нормальной работы слесарь должен производить заправку шабера через каждые 1,5 — 2 часа работы.
Шаберы с пластинами из твердого сплава затачивают на круге-«КЗ» (карбид кремния зеленый), а доводку производят на вращающемся чугунном или медном диске, на поверхность которого наносят карбид бора, разведенный в керосине. Заправку этих шаберов можно также производить и на чугунной плите, смазанной мастикой карбида бора.
Краска для шабрения. Шабровочная краска, которая наносится на поверхность контрольной плиты и служит для контроля качества шабрения детали или изделия, приготовляется в виде смеси машинного масла и краски (лазури, ультрамарина или сажи).
При приготовлении следует краску растереть с маслом так, чтобы не ощущалось никаких следов зерен и чтобы она не была слишком жидкой, так как излишек масла будет расплываться на контрольной плите, что затруднит проверку шабруемой поверхности.
Наиболее распространен прием нанесения краски на контрольную плиту с помощью мешочка, изготовленного из холста. В этот мешочек накладывают краску, мешочек завязывают и им натирают плиту. Краска выступает через поры мешочка и покрывает плиту тонким равномерным слоем.
предыдущая страница | Содержание | следующая страница |