На главную
3. ФОРМЫ ЛИТЬЯ ПОД ДАВЛЕНИЕМ
За последние годы в промышленности широко применяется литье под давлением — высокопроизводительный способ отливки деталей различного назначения. Детали или изделия, отлитые этим способом, в основном не требуют дальнейшей механической или слесарной обработки.
Отливку деталей производят в стальные формы на специальных машинах. По конструкции формы бывают одноместные и многоместные.
При массовом производстве наиболее выгодно отливку производить в многоместные формы. В результате быстрой кристаллизации металла он приобретает мелкозернистость, гладкие наружные поверхности отлитых деталей хорошо противостоят коррозии.
Способ литья под давлением заключается в том, что расплавленный металл или сплав под большим давлением и с большой скоростью из камеры сжатия подается поршнем в стальную форму.
Качество отливаемых деталей зависит от температуры и свойств металла и формы, в которую производится отливка.
Формы литья под давлением конструируются так, чтобы их можно было легко разнимать. Каждая форма состоит из двух частей, образуя полое рабочее пространство. Одна половина формы, на которой расположен литник при отливке, закрепляется на литейной машине и называется передней матрицей. Другая половина называется задней или подвижной матрицей.
Высокая точность изготовления формы дает возможность получать отлитые детали без припусков на механическую или слесарную обработку. Форма литья состоит из таких основных частей: матриц, стержней, вкладышей и устройства для выталкивания деталей.
Подвижные рабочие части формы называются стержнями. Они предназначены для образования полых пространств в отливке. На подвижной матрице при раскрытии формы остается отлитая деталь, которая удаляется при помощи выталкивателей ручных или автоматических.
В матрице закреплены все неподвижные части, в них же находятся направляющие отверстия для подвижных стержней. Неподвижная матрица крепится на специальной опорной плите машины. Подвижная — на подставке, на которой расположены сборные плиты для стержней, выталкивателей и других деталей.
Форма литья под давлением работает в сложных условиях. Она воспринимает на себя удары струи заливаемого в нее металла, который кроме теплового и механического воздействия оказывает еще и химическое. Поэтому для изготовления деталей для формы, соприкасающейся с расплавленным металлом, применяют жаростойкие легированные стали. Наиболее приемлемой сталью для этого является сталь марки ЗХ2В8 по ГОСТ 5950-51.
Все рабочие детали формы подвергают закалке до твердости Rc = 45 — 46. Кроме этого, для увеличения стойкости форм применяют азотирование, которое придает поверхностному слою рабочей части формы повышенную твердость, при сохранении пониженной твердости сердцевины деталей формы.
Для предохранения от налипания и приварки на рабочие поверхности формы жидкого металла производят оксидирование поверхностей форм. Во избежание заклинивания при нагреве формы подвижные части изготовляют с соответствующим зазором в плитах формы. Величина зазора определяется в каждом случае на основе опыта.
Для продления срока службы формы необходимо строго придерживаться определенной температуры нагрева формы, которую регулируют в процессе эксплуатации.
На фиг. 112 показана форма для литья, а на фиг. 113 — общий вид четырехместной формы для литья под давлением.
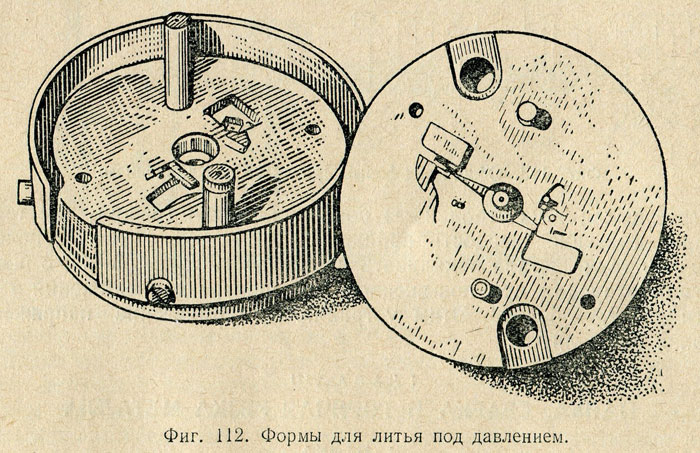
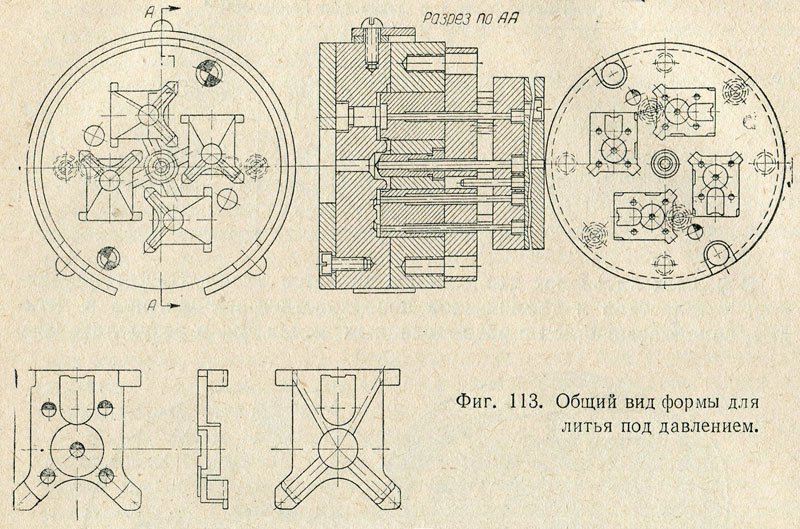
Все, что было изложено о стойкости штампов, в равной степени относится и к формам литья и прессформам. Чистота обработки рабочих частей форм литья и прессформ влияет на стойкость их еще в большей степени, чем в штампах. На стойкость прессформ и особенно форм литья под давлением большое влияние оказывает теплостойкость стали рабочих частей формы и выбор режима термической обработки.
Стойкость форм литья под давлением для различных металлов приводится в табл. 12.
Таблица 12
Стойкость форм для литья под давлением*
Сплавы | Стойкость форм (количество | |
Средняя | Максимальная | |
Цинковые | 10000 | 250000 |
*Данные взяты из книги В. М. Пляцкого, Технология литья под давлением, Машгиз, 1949. |
В формах литья под давлением в процессе эксплуатации появляется усталостное и термическое поверхностное напряжение в деталях, соприкасающихся с расплавленным металлом, в результате чего
цветных на поверхности этих деталей появляются сетчатые мелкие трещины, постепенно расширяющиеся и углубляющиеся.
Для предотвращения этого явления необходимо не только соблюдать строгий температурный режим работы формы (подогрев формы, температура заливаемого жидкого металла и т. д.), но периодически подвергать форму отпуску (искусственному старению) для снятия термических и усталостных напряжений. Необходимо отметить, что стремление к высокой твердости деталей форм литья, соприкасающихся с жидким металлом, не всегда целесообразно.
Практикой установлено, что рабочие детали формы, будучи изготовленными из стали марок ЗХ2В8, 5ХНТ или другой высоколегированной стали, имея твердость после термообработки Rc = 55 — 60, быстрее выходят из строя из-за появления сетки трещин, чем те же детали, имеющие твердость порядка Rc = 40 — 48. Поэтому целесообразней такие детали закаливать на твердость Rc = 58 — 60 с последующим отпуском при повышенной температуре для снижения твердости до Rc = 40 — 48. Этим устраняются термические напряжения деталей форм литья.
предыдущая страница | Содержание | следующая страница |